Photocurable Carbon Nanotube/Polymer Nanocomposite for the 3D Printing of Flexible Capacitive Pressure Sensors
- PMID: 38139958
- PMCID: PMC10747156
- DOI: 10.3390/polym15244706
Photocurable Carbon Nanotube/Polymer Nanocomposite for the 3D Printing of Flexible Capacitive Pressure Sensors
Abstract
A photocurable resin/carbon nanotube (CNT) nanocomposite was fabricated from aligned CNTs in an acrylic matrix. The conductivity of the nanocomposite increased rapidly and then stabilized when the CNT content was increased up to and beyond the percolation threshold. Various structures were created using a digital light processing (DLP) 3D printer. Various polymeric dispersants (SMA-amide) were designed and synthesized to improve the CNT dispersion and prevent aggregation. The benzene rings and lone electron pairs on the dispersant interacted with aromatic groups on the CNTs, causing the former to wrap around the latter. This created steric hindrance, thereby stabilizing and dispersing the CNTs in the solvent. CNT/polymer nanocomposites were created by combining the dispersant, CNTs, and a photocurable resin. The CNT content of the nanocomposite and the 3D printing parameters were tuned to optimize the conductivity and printing quality. A touch-based human interface device (HID) that utilizes the intrinsic conductivity of the nanocomposite and reliably detects touch signals was fabricated, enabling the free design of sensors of various styles and shapes using a low-cost 3D printer. The production of sensors without complex circuitry was achieved, enabling novel innovations.
Keywords: 3D printing; capacitive pressure sensor; carbon nanotubes; photocuring; sensing element.
Conflict of interest statement
The authors declare no conflict of interest.
Figures
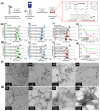
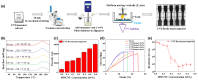
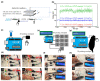
Similar articles
-
Polymer Composite Containing Carbon Nanotubes and their Applications.Recent Pat Nanotechnol. 2017 Jul 10;11(2):109-115. doi: 10.2174/1872210510666161027155916. Recent Pat Nanotechnol. 2017. PMID: 27978788
-
Photocurable Polymer-Based 3D Printing: Advanced Flexible Strain Sensors for Human Kinematics Monitoring.Polymers (Basel). 2023 Oct 20;15(20):4170. doi: 10.3390/polym15204170. Polymers (Basel). 2023. PMID: 37896414 Free PMC article.
-
Solvent-Free and Cost-Efficient Fabrication of a High-Performance Nanocomposite Sensor for Recording of Electrophysiological Signals.Biosensors (Basel). 2024 Apr 11;14(4):188. doi: 10.3390/bios14040188. Biosensors (Basel). 2024. PMID: 38667181 Free PMC article.
-
Carbon Nanotubes and Carbon Nanotube Structures Used for Temperature Measurement.Sensors (Basel). 2019 May 29;19(11):2464. doi: 10.3390/s19112464. Sensors (Basel). 2019. PMID: 31146463 Free PMC article. Review.
-
Review on Conductive Polymer/CNTs Nanocomposites Based Flexible and Stretchable Strain and Pressure Sensors.Sensors (Basel). 2021 Jan 6;21(2):341. doi: 10.3390/s21020341. Sensors (Basel). 2021. PMID: 33419047 Free PMC article. Review.
Cited by
-
Sandwich-Structured Carbon Nanotube Composite Films for Multifunctional Sensing and Electrothermal Application.Polymers (Basel). 2024 Sep 1;16(17):2496. doi: 10.3390/polym16172496. Polymers (Basel). 2024. PMID: 39274129 Free PMC article.
-
Flexible Sensors Based on Conductive Polymer Composites.Sensors (Basel). 2024 Jul 18;24(14):4664. doi: 10.3390/s24144664. Sensors (Basel). 2024. PMID: 39066060 Free PMC article. Review.
-
Advancements and Applications of Micro and Nanostructured Capacitive Sensors: A Review.Sens Actuators A Phys. 2024 Oct 16;377:115701. doi: 10.1016/j.sna.2024.115701. Epub 2024 Jul 11. Sens Actuators A Phys. 2024. PMID: 39129941
References
-
- Huang C.Y., Chiu C.W. Facile fabrication of a stretchable and flexible nanofiber carbon film-sensing electrode by electrospinning and its application in smart clothing for ECG and EMG monitoring. ACS Appl. Electron. Mater. 2021;3:676–686. doi: 10.1021/acsaelm.0c00841. - DOI
-
- Cui W., Yang Y., Di L., Dababneh F. Additive manufacturing-enabled supply chain: Modeling and case studies on local, integrated production-inventory-transportation structure. Addit. Manuf. 2021;48:102471. doi: 10.1016/j.addma.2021.102471. - DOI
Grants and funding
LinkOut - more resources
Full Text Sources