Design and implementation of a jellyfish otolith-inspired MEMS vector hydrophone for low-frequency detection
- PMID: 34567721
- PMCID: PMC8433173
- DOI: 10.1038/s41378-020-00227-w
Design and implementation of a jellyfish otolith-inspired MEMS vector hydrophone for low-frequency detection
Abstract
Detecting low-frequency underwater acoustic signals can be a challenge for marine applications. Inspired by the notably strong response of the auditory organs of pectis jellyfish to ultralow frequencies, a kind of otolith-inspired vector hydrophone (OVH) is developed, enabled by hollow buoyant spheres atop cilia. Full parametric analysis is performed to optimize the cilium structure in order to balance the resonance frequency and sensitivity. After the structural parameters of the OVH are determined, the stress distributions of various vector hydrophones are simulated and analyzed. The shock resistance of the OVH is also investigated. Finally, the OVH is fabricated and calibrated. The receiving sensitivity of the OVH is measured to be as high as -202.1 dB@100 Hz (0 dB@1 V/μPa), and the average equivalent pressure sensitivity over the frequency range of interest of the OVH reaches -173.8 dB when the frequency ranges from 20 to 200 Hz. The 3 dB polar width of the directivity pattern for the OVH is measured as 87°. Moreover, the OVH is demonstrated to operate under 10 MPa hydrostatic pressure. These results show that the OVH is promising in low-frequency underwater acoustic detection.
Keywords: Engineering; Physics.
© The Author(s) 2021.
Conflict of interest statement
Conflict of interestThe authors declare that they have no conflict of interest.
Figures
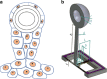
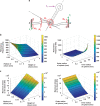
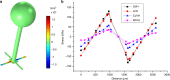
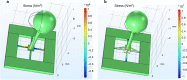
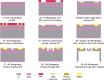
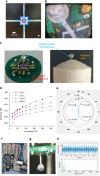
Similar articles
-
Design and Simulation of Flexible Underwater Acoustic Sensor Based on 3D Buckling Structure.Micromachines (Basel). 2021 Dec 10;12(12):1536. doi: 10.3390/mi12121536. Micromachines (Basel). 2021. PMID: 34945387 Free PMC article.
-
The Development of the Differential MEMS Vector Hydrophone.Sensors (Basel). 2017 Jun 8;17(6):1332. doi: 10.3390/s17061332. Sensors (Basel). 2017. PMID: 28594384 Free PMC article.
-
Design and Implementation of a Four-Unit Array Piezoelectric Bionic MEMS Vector Hydrophone.Micromachines (Basel). 2024 Apr 14;15(4):524. doi: 10.3390/mi15040524. Micromachines (Basel). 2024. PMID: 38675335 Free PMC article.
-
Research on Direction of Arrival Estimation Based on Self-Contained MEMS Vector Hydrophone.Micromachines (Basel). 2022 Jan 30;13(2):236. doi: 10.3390/mi13020236. Micromachines (Basel). 2022. PMID: 35208360 Free PMC article.
-
Fabrication and Underwater Testing of a Vector Hydrophone Comprising a Triaxial Piezoelectric Accelerometer and Spherical Hydrophone.Sensors (Basel). 2022 Dec 13;22(24):9796. doi: 10.3390/s22249796. Sensors (Basel). 2022. PMID: 36560165 Free PMC article.
Cited by
-
In-silico study on perovskites application in capturing and distorting coronavirus.Inform Med Unlocked. 2021;26:100755. doi: 10.1016/j.imu.2021.100755. Epub 2021 Oct 10. Inform Med Unlocked. 2021. PMID: 34660882 Free PMC article.
-
High-Sensitivity Piezoelectric MEMS Accelerometer for Vector Hydrophones.Micromachines (Basel). 2023 Aug 14;14(8):1598. doi: 10.3390/mi14081598. Micromachines (Basel). 2023. PMID: 37630134 Free PMC article.
-
Dual Band MEMS Directional Acoustic Sensor for Near Resonance Operation.Sensors (Basel). 2022 Jul 28;22(15):5635. doi: 10.3390/s22155635. Sensors (Basel). 2022. PMID: 35957192 Free PMC article.
-
Design and Simulation of Flexible Underwater Acoustic Sensor Based on 3D Buckling Structure.Micromachines (Basel). 2021 Dec 10;12(12):1536. doi: 10.3390/mi12121536. Micromachines (Basel). 2021. PMID: 34945387 Free PMC article.
-
Microfluidics for Cancer Biomarker Discovery, Research, and Clinical Application.Adv Exp Med Biol. 2022;1379:499-524. doi: 10.1007/978-3-031-04039-9_20. Adv Exp Med Biol. 2022. PMID: 35761005
References
-
- Testa C, Greco L. Prediction of submarine scattered noise by the acoustic analogy. J. Sound Vib. 2018;426:186–218. doi: 10.1016/j.jsv.2018.04.011. - DOI
-
- Yildiz S, Dorman LM, Kuperman WA. Using hydrophones as vector sensors. J. Acoust. Soc. Am. 2014;135:2361–2364. doi: 10.1121/1.4877778. - DOI
-
- Ma R, Zhang WT, Li F. Two-axis slim fiber laser vector hydrophone. IEEE Photon. Techol. Lett. 2011;23:335–337. doi: 10.1109/LPT.2011.2104413. - DOI
-
- Di Iorio L, Gervaise C, Jaud V. Hydrophone detects cracking sounds: non-intrusive monitoring of bivalve movement. J. Exp. Mar. Biol. Ecol. 2014;432:9–16.
LinkOut - more resources
Full Text Sources
Other Literature Sources
Miscellaneous