Advances in Capacitive Micromachined Ultrasonic Transducers
- PMID: 30813447
- PMCID: PMC6412242
- DOI: 10.3390/mi10020152
Advances in Capacitive Micromachined Ultrasonic Transducers
Abstract
Capacitive micromachined ultrasonic transducer (CMUT) technology has enjoyed rapid development in the last decade. Advancements both in fabrication and integration, coupled with improved modelling, has enabled CMUTs to make their way into mainstream ultrasound imaging systems and find commercial success. In this review paper, we touch upon recent advancements in CMUT technology at all levels of abstraction; modeling, fabrication, integration, and applications. Regarding applications, we discuss future trends for CMUTs and their impact within the broad field of biomedical imaging.
Keywords: acoustics; capacitive; capacitive micromachined ultrasonic transducer (CMUT); fabrication; micromachining; modelling; transducer.
Conflict of interest statement
B.T. Khuri–Yakub serves as a technical advisor for Butterfly Network. The other authors declare no conflict of interest.
Figures
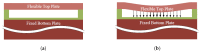


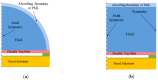
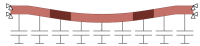
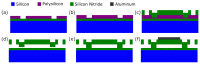
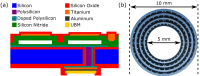
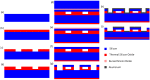
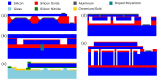
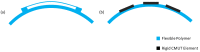
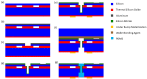
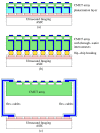
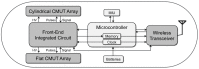
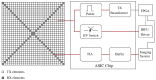
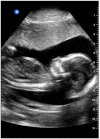
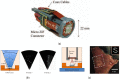

Similar articles
-
Capacitive micromachined ultrasonic transducers: fabrication technology.IEEE Trans Ultrason Ferroelectr Freq Control. 2005 Dec;52(12):2242-58. doi: 10.1109/tuffc.2005.1563267. IEEE Trans Ultrason Ferroelectr Freq Control. 2005. PMID: 16463490
-
Applications of Capacitive Micromachined Ultrasonic Transducers: A Comprehensive Review.IEEE Trans Ultrason Ferroelectr Freq Control. 2022 Feb;69(2):456-467. doi: 10.1109/TUFFC.2021.3112917. Epub 2022 Jan 27. IEEE Trans Ultrason Ferroelectr Freq Control. 2022. PMID: 34520356 Review.
-
Capacitive micromachined ultrasonic transducers for medical imaging and therapy.J Micromech Microeng. 2011 May;21(5):54004-54014. doi: 10.1088/0960-1317/21/5/054004. J Micromech Microeng. 2011. PMID: 21860542 Free PMC article.
-
Fabrication of 2-D Capacitive Micromachined Ultrasonic Transducer (CMUT) Array through Silicon Wafer Bonding.Micromachines (Basel). 2022 Jan 8;13(1):99. doi: 10.3390/mi13010099. Micromachines (Basel). 2022. PMID: 35056263 Free PMC article.
-
cMUT technology developments.Z Med Phys. 2023 Aug;33(3):256-266. doi: 10.1016/j.zemedi.2023.04.010. Epub 2023 Jun 12. Z Med Phys. 2023. PMID: 37316428 Free PMC article. Review.
Cited by
-
Research on Broadband Matching Method for Capacitive Micromachined Ultrasonic Transducers Based on PDMS/TiO2 Particles.Micromachines (Basel). 2022 Oct 26;13(11):1827. doi: 10.3390/mi13111827. Micromachines (Basel). 2022. PMID: 36363848 Free PMC article.
-
A Review on Analytical Modeling for Collapse Mode Capacitive Micromachined Ultrasonic Transducer of the Collapse Voltage and the Static Membrane Deflections.Micromachines (Basel). 2021 Jun 18;12(6):714. doi: 10.3390/mi12060714. Micromachines (Basel). 2021. PMID: 34207176 Free PMC article. Review.
-
Design and Finite Element Simulation of a Novel 3D-CMUT Device for Simultaneous Sensing of In-Plane and Out-of-Plane Displacements of Ultrasonic Guided Waves.Sensors (Basel). 2023 Oct 25;23(21):8706. doi: 10.3390/s23218706. Sensors (Basel). 2023. PMID: 37960406 Free PMC article.
-
Ultra-Low-Voltage Capacitive Micromachined Ultrasonic Transducers with Increased Output Pressure Due to Piston-Structured Plates.Micromachines (Basel). 2022 Apr 26;13(5):676. doi: 10.3390/mi13050676. Micromachines (Basel). 2022. PMID: 35630143 Free PMC article.
-
Research on Novel CMUTs for Detecting Micro-Pressure with Ultra-High Sensitivity and Linearity.Micromachines (Basel). 2021 Oct 30;12(11):1340. doi: 10.3390/mi12111340. Micromachines (Basel). 2021. PMID: 34832751 Free PMC article.
References
-
- Haller M.I., Khuri-Yakub B.T. A Surface Micromachined Electrostatic Ultrasonic Air Transducer. IEEE Trans. Ultrason. Ferroelectr. Freq. Control. 1996;43:1–6. doi: 10.1109/58.484456. - DOI
-
- Soh H.T., Ladabaum I., Atalar A., Quate C.F., Khuri-Yakub B.T. Silicon micromachined ultrasonic immersion transducers. Appl. Phys. Lett. 1996;69:3674–3676. doi: 10.1063/1.117185. - DOI
-
- Mason W.P. Electromechanical Transducers and Wave Filters. D. Van Nostrand; New York, NY, USA: 1942.
Publication types
Grants and funding
LinkOut - more resources
Full Text Sources