Inertial Navigation Systems
AI-Driven Navigation Systems for GNSS and GNSS-Denied Environments
Advanced Navigation is one of the largest inertial navigation systems (INS) manufacturers. Our range of MEMS and FOG-based inertial navigation systems provide accurate position, velocity, acceleration, and orientation under the most demanding conditions. They combine temperature-calibrated accelerometers, gyroscopes, magnetometers, and pressure sensors with state-of-the-art RTK GNSS receivers. These are coupled in an AI-based algorithm to deliver the highest performance for the lowest SWaP-C (Size, Weight, Power Consumption, Cost).
This proprietary algorithm increases the INS accuracy by tracking sensor errors faster than the traditional Kalman filter. With many traditional inertial navigation systems, basic linear constraints are applied to position, velocity and acceleration. In contrast, the Advanced Navigation AI-based algorithm applies far more thorough dynamic constraints with full physics models of vehicle motion, allowing for better tracking of errors, more reliable data, and higher accuracy.
Advanced Navigation inertial navigation systems contain reliable sensors that are each subject to an intensive 8-hour temperature-based calibration process. This provides the highest accuracy possible for each sensor class over the full operating temperature range from -40° C to 85° C.
The GNSS receivers support all current navigational satellite constellations, including GPS, GLONASS, GALILEO, BeiDou and QZSS.
A high internal filter rate of 1000 Hz ensures high dynamic performance in the most demanding applications.
The INS range covers four critical performance grades (industrial, tactical, navigation and strategic) enabling clients to use a single supplier for multiple application and accuracy needs.
Thanks to vertical integration, Advanced Navigation has total control over both hardware manufacturing and software design, enabling us to set a new benchmark for accurate and reliable navigation and positioning.
Advanced Navigation INS products are used by many of the world’s leading companies for both commercial and defence applications. Our global team of support engineers ensures that our solutions are successfully integrated into your systems.
Our INS Solutions
From industrial to strategic grade, our broad range of inertial navigation systems delivers unprecedented performance in each class. All Advanced Navigation INS use a common communication protocol, enabling customers to extend their product range by moving up or down the accuracy spectrum without incurring re-engineering costs.
MEMS GNSS/INS
Spatial
Single antenna MEMS INS
Roll & Pitch
0.1 °
Heading (GNSS)
0.2 °
Bias Instability
3 °/hr
Position Accuracy
20 mm
View Solution
Certus Mini N
Navigation, single antenna
Roll & Pitch
0.1 °
Heading (Velocity)
0.2 °
RTK Positioning
10 mm
Update Rate
1000 Hz
View Solution
Certus Mini D
Dual-antenna Navigation
Roll & Pitch
0.1 °
Heading (GNSS)
0.1 °
RTK Positioning
10 mm
Update Rate
1000 Hz
View Solution
Certus
Market-leading dual antenna INS
Roll & Pitch
0.1 °
Heading (GNSS)
0.1 °
Bias Instability
3 °/hr
Position Accuracy
10 mm
View Solution
Certus Evo
Ultra-high accuracy MEMS INS
Roll & Pitch
0.03 °
Heading (GNSS)
0.05 °
Bias Instability
0.2 °/hr
Position Accuracy
10 mm
View Solution
FOG GNSS/INS
Spatial FOG Dual
Industry-proven FOG INS
Roll & Pitch
0.01 °
Heading (GNSS)
0.01 °
Bias Instability
0.1 °/hr
Position Accuracy
10 mm
View Solution
Boreas D70 & D90
World-first digital FOG technology
D70
D90
Roll & Pitch
0.01 °
0.005 °
Heading (Gyrocompass)
0.1 ° seclat
0.01 ° seclat
Bias Instability
0.01 °/hr
0.001 °/hr
Position Accuracy
10 mm
10 mm
View Solution
Satellite Compass
GNSS Compass
Plug-and-play GNSS/INS navigation and heading solution
Roll & Pitch
0.4 °
Position Accuracy (RTK)
0.01 m
Heading
0.2 °
Update Rate
200 Hz
View Solution
The Latest News, Articles & More
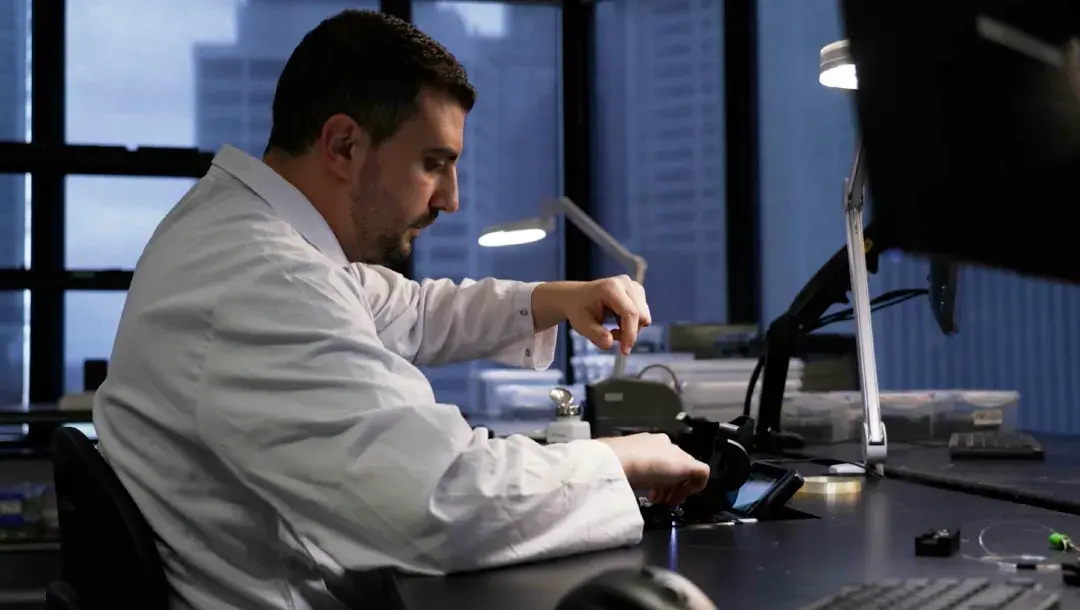
Decoding Earth’s Fingerprints: Advanced Navigation and MBDA Collaborate on Breakthrough Resilient Navigation Technology
20 November 2024
Go to Article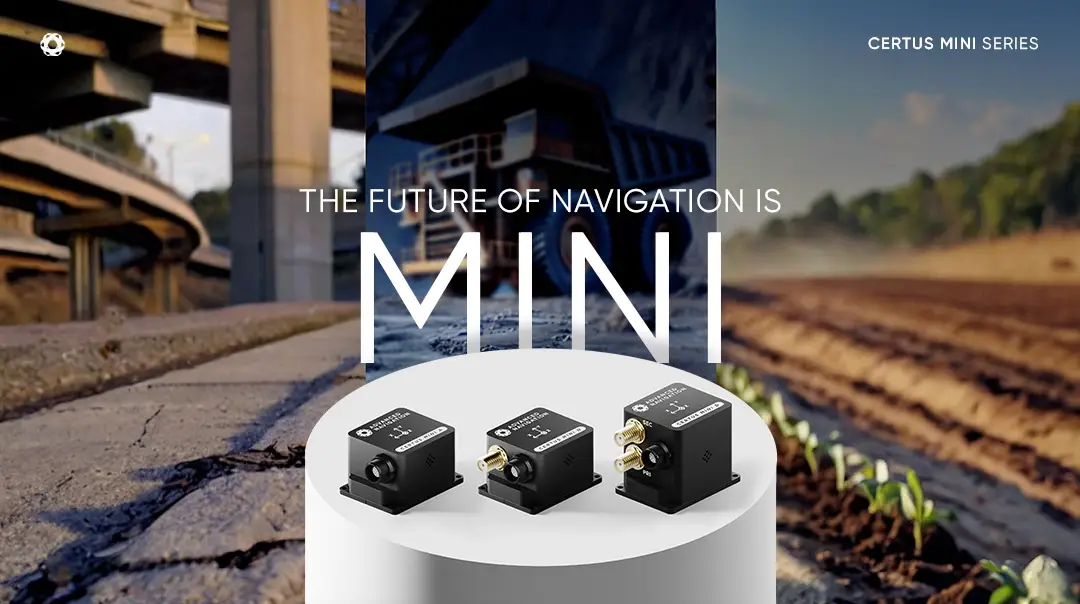
The Future of Navigation is Mini: Unveiling the Certus Mini Series with INS and AHRS
25 September 2024
Go to ArticleCommon Questions about INS
What is an inertial navigation system?
An Inertial Navigation System, also known as an INS, is a navigation solution that measures changes in motion through inertial sensors in order to determine the velocity, orientation, and position of an object.
How does an inertial navigation system work? Does it include an inertial measurement unit and GNSS receiver?
The IMU within the inertial navigation system is composed of inertial sensors including accelerometers, gyroscopes, and often, magnetometers.
More details:
- Accelerometers are sensors that measure the acceleration of an object, tracking the changing velocity.
- Gyroscopes are rotation sensors that measure the changes in the angular velocity of an object.
- Magnetometers measure the strength and direction of the Earth’s magnetic field to determine the orientation with respect to the magnetic North Pole. The inertial navigation system will correct for the difference between the true north and the magnetic north. However, in most vehicles, the accuracy of a magnetometer is affected by magnetic interference sources.
Each of these sensors has its own limitations, which is why they work better when they are combined. By measuring these three sensors, the inertial navigation system is able to calculate any distance travelled and the heading.
By doing so, an inertial navigation system is capable of measuring:
- Pitch
- Roll
- Heading
An INS also incorporates a GNSS receiver which is used as an additional sensor. By doing so, It gives an absolute position rather than a relative position. An INS alone can determine a position relative to the inertial frame of reference, but combined with GNSS it can provide absolute position by accurately providing the global position.
INS and GNSS: What’s the difference?
An inertial navigation system is a self-contained system that doesn’t rely on satellite signals or base stations to calculate position.
A GNSS requires information from satellites to determine positioning. The use of GNSS is quite common in civilian, commercial, and defence applications with varying degrees of navigational accuracy. However, GNSS is subject to several modes of interference, including atmospheric disruption and multipathing. GNSS signals can also be lost due to obstructions like tunnels or intentional interference such as jamming and spoofing which is possible in military applications.
Working in tandem, the two navigation systems can be used to provide highly accurate positions, with an inertial navigation system able to calculate position should the vehicle enter a GNSS-denied environment, effectively improving GNSS navigation information.
What methods can be used to improve the performance of an INS (RTK, odometer, Air Data Unit, DVL)?
The accuracy of an INS can be further improved through the use of external aiding sensors. Input from these sensors is used as additional data for the sensor fusion algorithm to better estimate position, velocity and orientation.
The type of aiding sensors used with an INS will largely depend on the application. Some examples of aiding sensors include:
- Wheel Speed Sensor – Land Application – Measures vehicle speed through wheel rotation.
- OBDII Odometer – Land Application – Communicates with a vehicle onboard computer to provide vehicle speed to the INS.
- Air Data Unit – Air Application – Measures pitot airspeed and barometric altitude.
- Doppler Velocity Log (DVL) – Subsea Application – This is an acoustic sensor that estimates velocity relative to the sea floor.
All Advanced Navigation INS solutions can interface with a wide range of sensing technologies to improve performance.
What is an inertial measurement unit?
An INS consists of an Inertial Measurement Unit (IMU) and a computational unit. By using a known starting position and known orientation (referred to as an inertial frame of reference) the IMU will track changes in velocity and rotation applied to an object and feed that raw data to the computational unit in the INS, so it can establish the new position and orientation accurately.
What are the benefits of using an inertial navigation system?
Inertial navigation systems are proven solutions that provide position data. There are different types of inertial navigation systems, ranging from lightweight MEMS (micro-electromechanical systems) to more dynamic fibre optic gyroscopes (FOG), and more advanced digital fibre optic gyroscopes (DFOG).
An inertial navigation system is particularly beneficial in a GNSS-denied (global navigation satellite system) environment. GNSS can be interfered with in underground environments like tunnels or underwater environments. GNSS signals can also be interfered with by way of multi-pathing or atmospheric interference. While this may be an inconvenience for navigation on a phone, for the likes of aerial surveying or defence applications, positioning requires no room for error.
This is why an inertial navigation system that integrates a GNSS is far more reliable, as an INS by nature mitigates the room for error a GNSS would experience alone. An inertial navigation system can operate effectively and accurately without communicating to a base station, making it well suited where GNSS is either susceptible to inaccuracies or isn’t available at all.
How accurate is an inertial navigation system?
There are many kinds of inertial navigation systems, all of which have varying degrees of accuracy.
High-end INS that utilize fibre optic gyroscope (FOG) are accurate within centimeters and would be used for aerospace exploration, AUVs, and defence applications. Unlike GNSS, inertial navigation systems are immune to jamming or spoofing as they don’t require references from external sources like satellites or base stations.
How is an INS calibrated and tested?
An INS calibration is important in ensuring that the sensor output results are accurate and repeatable within the specified operating conditions. Calibration is the process of comparing INS outputs with reference information and determining co-efficiency factors that need to be applied that the two match.
The output measurement of an INS can vary according to several factors, such as:
- Temperature – affects the output result of an INS when subject to a wide range of temperatures.
- Systematic error sources from accelerometers and gyroscopes such as:
- sensors bias
- sensor output scale factor
- sensor cross-axis sensitivity
- misalignment of sensor axis
- MEMS gyroscope G sensitivity
- Magnetic Field – Some INS units have a magnetometer sensor to help determine the heading. When an INS is subject to changes in the magnetic field (for example, by ferrous objects and magnets, which is known as static interference), the magnetometer output will vary. Typically, this type of error is calibrated once the INS has been installed in the final installation position on a vehicle to take into account all sources of static magnetic interference. All Advanced Navigation INS and AHRS systems have built-in magnetic calibration software to help counter this problem.
An INS can be calibrated to counter the abovementioned issues to produce accurate and repeatable results by utilizing equipment such as temperature chambers, leveling tables, rate tables and gimbals. All Advanced Navigation INS & AHRS products are calibrated, tested and checked for conformance to relevant industry standards before leaving the factory.
How accurate are inertial navigation sensors?
INS sensors can be classified into five performance grades (see details below), primarily based on gyroscope performance.
While an INS will also have other sensors such as accelerometers and magnetometers, the cost vs performance of the gyroscope is primarily what is used to determine the performance grade. For example, MEMS-based INS performance typically ranges from consumer to tactical grade. However, with recent advances in MEMS and data fusion technologies, we are now seeing MEMS-based INS performance approach the high-end tactical grade.
Performance grade: Consumer/Automotive
- Gyro Bias Stability: over 20 °/h
- Cost: $
- Example Applications: Motion detection
- Sensor Technology: MEMS
- Advanced Navigation Products: –
Performance grade: Industrial/Tactical
- Gyro Bias Stability: 5 – 20 °/h
- Cost: $$
- Example Applications: Robotics and industrial applications
- Sensor Technology: MEMS
- Advanced Navigation Products: GNSS Compass
Performance grade: High-End Tactical
- Gyro Bias Stability: 0.1 – 5 °/h
- Cost: $$$
- Example Applications: Platform stablization and autonomous systems
- Sensor Technology: MEMS / FOG (Fibre-optic gyroscope) /RLG (Ring laser gyroscope)
- Advanced Navigation Products: Spatial, Certus, Certus Evo
Performance grade: Navigation
- Gyro Bias Stability: 0.01 – 0.1 °/h
- Cost: $$$$
- Example Applications: Aircraft/maritime navigation
- Sensor Technology: FOG/RLG
- Advanced Navigation Products: Spatial FOG, Spatial FOG Dual
Performance grade: Strategic
- Gyro Bias Stability: 0.0001 – 0.01 °/h
- Cost: $$$$$
- Example Applications: Submarine navigation
- Sensor Technology: FOG/RLG
- Advanced Navigation Products: Boreas