キュポラ存続へ脱炭素研究、バイオ燃料活用へ官民集結
鋳物に関わる28の企業・団体が、二酸化炭素(CO2)の排出が課題のキュポラ存続に向けた共同研究を4月から本格的に開始した。バイオ燃料の開発や原料の調達、製造方法の確立などを目指して2023年から活動しており、4月に日本鋳造協会(東京都港区)や経済産業省も加わった。28年までにバイオ燃料の実用化とコークスからの全量置き換えを目指す。(大阪・池知恵)
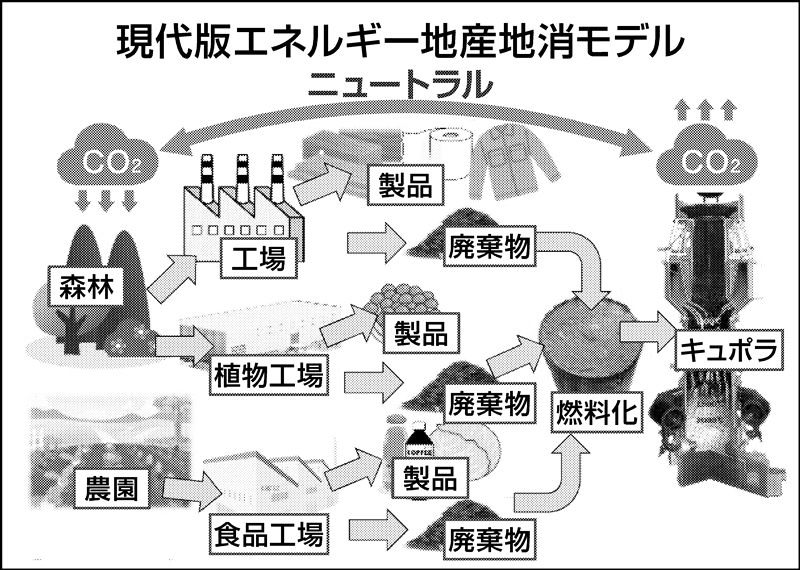
キュポラは石炭コークスを燃料に鉄スクラップを溶かす鋳物の基幹設備で、1970年には鋳鉄溶解量の8割以上を占めていた。ただ大量のCO2排出が課題で、最近では電気炉への移行が急速に進む。現在は4割程度まで減少している。
一方、電気炉にも課題はある。最大のネックは原料だ。高温に熱したコークスで亜鉛など不純物を除去できるキュポラと異なり、精錬効果が期待できない。不純物が残留すると鋳物の品質は低下し、使用できるスクラップが制限されてしまう。
マツダ技術本部パワートレイン技術部の田中裕一アシスタントマネージャーは、「大手企業が(鉄スクラップの)外部調達を増やせば市場価格の上昇や中小企業の調達に影響を与えかねない」と指摘する。マツダは本社工場(広島県府中町)のキュポラで使用する鉄スクラップの約4割を、プレス工場から発生する亜鉛メッキ鋼板で賄う。これを外部調達に切り替えると、20年前から2倍以上に上昇する国内の鉄スクラップ価格がさらに跳ね上がりかねない。
加えて電力市場への影響も無視できない。国内の全てのキュポラが電気炉に移行した場合、年間消費電力は16億8000万キロワット時に達する。これは出力35万キロワットの発電所1基分に相当する。
バイオ燃料などの研究に取り組むのは、23年に有志企業で立ち上げたキュポラカーボンニュートラル共創ワーキンググループだ。マツダや豊田自動織機、アイシン高丘など自動車業界のほか、水道管メーカーの栗本鉄工所、鋳造設備商社の大銑産業などが集結。成形方法や発熱量が異なる四つのバイオ燃料の研究開発に加え、原料調達、炭化・成形プロセスなど13の分科会で共同研究に取り組んでいる。
マツダは24年度内に本社工場の10トンキュポラの燃料をバイオ燃料に100%置換する実証を始める。強度や燃焼量がコークスに匹敵し、ベッドコークスとして活用可能なバイオ燃料「バイオ成形炭」を採用。炉底に詰めるベッドコークスは、下部にとどまり鉄源に炭素を与える重要な役割を果たす。全量の置き換えには、このベッドコークスの代替となるバイオ燃料が欠かせない。
すでに口径60ミリメートルのバイオ成形炭の試作開発に成功した。さらに同120ミリメートルの研究開発を進めるとともに、実証用にバイオ成形炭の製造設備導入を進めている。
栗本鉄工所はヤシ殻炭を粉砕したバイオ微粉炭や、そば殻を原料とするバイオコークスを実証中。二つのバイオ燃料を組み合わせ、化石燃料から最大35%の置き換えを目指す。エンジン部品の鋳造を手がけるコヤマ(長野市)は、キノコ栽培で発生する廃菌床を原料としたバイオ燃料を開発中だ。
バイオ燃料の実用化には、原材料の安定調達が欠かせない。しかし原料の多くは海外に頼っており、特に有力な原料であるヤシ殻炭の価格は高騰し、国内調達網の確立が課題だ。そこで有望視されるのがコーヒー殻や茶殻、廃パルプなどだ。清涼飲料や製紙は全国に工場が立地し、安定的に廃材を調達できる。バイオ燃料の製造も含め、「今後、異業種へも働きかけていきたい」(田中裕一アシスタントマネージャー)としており、業界の枠を超えた取り組みも今後の課題となる。