自動車部品メーカーが本腰、製造工程の脱炭素はここまで進んだ!
自動車部品メーカー各社が製造工程での二酸化炭素(CO2)排出削減に本腰を入れている。自動車業界は2050年に車の製造から廃棄までのライフサイクル全体でカーボンニュートラル(温室効果ガス排出量実質ゼロ)の実現を目指す。自動車メーカーだけでなく、サプライチェーン(供給網)全体で目標を達成するため、再生可能エネルギーの利用や加熱工程の廃止・削減などモノづくりの形を変革している。各社の動向を追った。(増田晴香)
曙ブレーキ工業は製造工程のCO2排出量と製造時間を従来比半分に抑えたブレーキパッドを、23年秋以降にアフターマーケットで発売する。パッド成形時の加熱や焼き付けなど高温処理にエネルギーを使っていたため、製法を見直し開発した製品だ。
工程の順序を入れ替えることで各工程での加熱を集約・統合した。また原材料の一部を変更することで、低温での成形も可能にした。先行摩擦材開発部の日下聡部長は「(同製法を)今後摩擦材全般に拡大することを検討する」と話す。工程を簡略化することで、時間の短縮や多品種少量品対応もしやすくなるという。
同製品はCO2だけでなく、製造時の粉塵発生量や臭気濃度、環境負荷物質を削減するなどさまざまな課題に対応した。また欧州の規制に対応し、ブレーキ使用時に発生する摩耗粉も減らす。アフターマーケット向けに投入した後、サプライチェーン全体の脱炭素化に貢献できる点を自動車メーカー向けにも提案し、新車への採用を目指す。
アーレスティは鋼板とアルミニウムダイカストを機械的に接合する際、接合面のみを部分加熱するレーザー熱処理技術を開発した。CO2排出量は従来の処理の10分の1、コストは4分の1に低減できると期待する。車両のボディー製造ラインで早期に同技術を用いたアルミ合金ダイカストの導入を目指す。
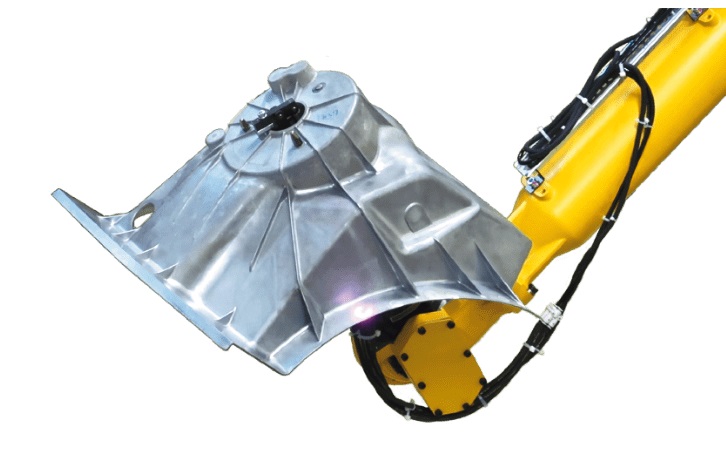
車両軽量化などでボディー部品にアルミダイカストを使用する際、多くはベース材となる鋼板との接合が必要になる。鋼板との接合で割れを防止するための熱処理である「T7処理」は、熱処理炉の加熱に多量のエネルギーを使用する。
新たなレーザー熱処理技術では、炉を使わず必要な部分のみに処理を施せる。また、短時間で割れを防ぐ「延性」を確保できる。
トピー工業が導入したインターナルカーボンプライシング制度(ICP制度)は、企業が脱炭素を推進するために、独自にCO2排出量に価格を付け、投資判断などに活用する仕組み。排出量を見える化し、経済的インセンティブを創出することで社内意識の変革、脱炭素への対応を促進する狙いだ。
同社では社内炭素価格を導入時は1トン当たり8200円としている。CO2排出量の増減を伴う、生産設備などへの投資や研究開発計画を対象に社内炭素価格を適用。費用換算したものを投資判断の参考とする。
同社は22―25年度の中期経営計画で、資本生産性指標の向上を目的にICP制度導入の検討を進めてきた。同制度を活用しサステナブル(持続可能)経営の基盤を強化する。
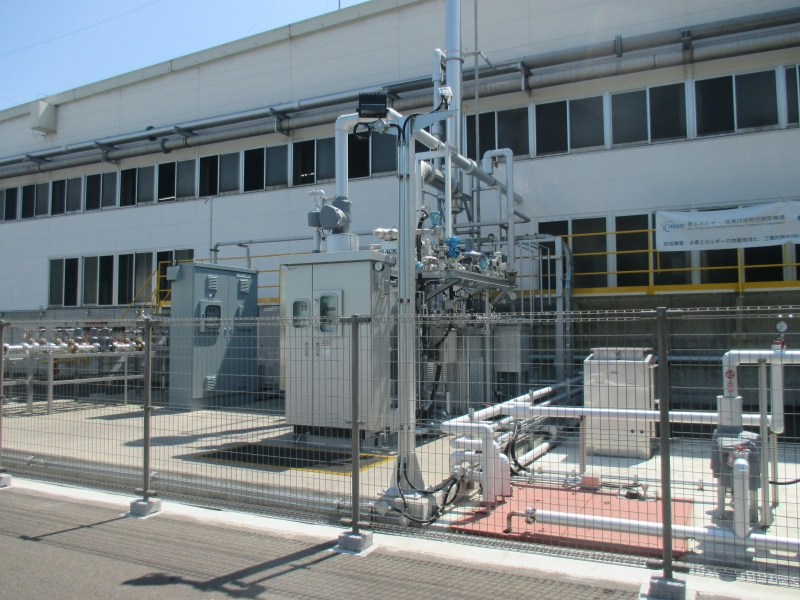
タイヤ各社も持続可能性に配慮した経営を掲げ、タイヤ製造のカーボンニュートラル化に向け先進的な取り組みを展開している。
住友ゴム工業は白河工場(福島県白河市)で、加硫工程で大量に使用する熱(蒸気)をつくるボイラの燃料に水素を活用している。これまでは天然ガスを利用していた。1月には、水素エネルギーと太陽光発電によるエネルギーを活用し、製造時の直接排出量「スコープ1」と間接排出量「スコープ2」においてカーボンニュートラルを達成する量産タイヤの生産を開始した。
同時に福島県内で生産する水素の地産地消モデルの確立も進めている。レゾナック・ガスプロダクツ(川崎市幸区)の福島県郡山市の拠点から供給を受けているほか、7月末から約1カ月間、水素製造施設「福島水素エネルギー研究フィールド(FH2R)」(同浪江町)から再生エネなどを使用して製造した水素を調達している。
水素活用は今後白河工場全体、国内工場全体に拡大する計画。30年にCO2半減の目標に対し、1年前倒しの29年に達成の見込みだ。
ブリヂストンは24―26年の次期中期経営計画で、工場の生産性を高める「スマート化」と生産量当たりのエネルギー消費量を低減する「グリーン化」を検討している。同社はグローバルでの再生エネ比率(電力)を23年に50%以上、30年までに100%達成を掲げている。4月までにタイヤ・原材料の国内10工場で使用する全ての購入電力を再生エネに切り替えた。
工場のグリーン化では再生エネの利用拡大に加え「省エネルギー活動もしていかなくてはビジネスの持続性を担保できない」(石橋秀一グローバル最高経営責任者〈CEO〉)と認識。今後はエネルギーを多く使用する加熱工程など、モノづくりの工程全体を見直す構えだ。
【関連記事】 苦悩する自動車部品メーカーが頼りにする育成所