取り組みの概要
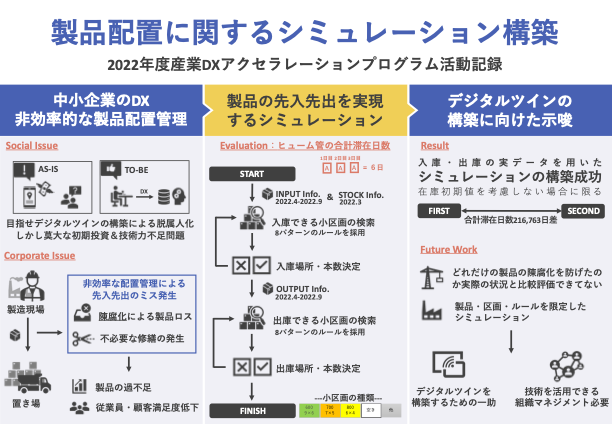
背景と目的
現在我が国では、データやデジタル技術を使って、顧客目線で新たな価値を創造するデジタルトランスフォーメーション(以下、DX)の促進が求められている。DXはデジタル技術による業務効率化に留まらず企業文化やビジネスモデルまでを含む大きな変革を目指すものであり、成功させるためにはその導入プロセスも非常に重要となる。
このような背景の中で、DXの手法の一つとしてデジタルツインが注目を浴びている。デジタルツインとは、物理空間の仕組み等をそのままバーチャル空間で再現し、リアルタイム・予測的にシミュレーションを行う技術である。これは物流業や製造業等の製品や在庫を保有する事業形態での期待が高まっている。
一方、デジタルツインの構築には、技術力を有する人材の確保とシステムに対する初期投資が必要なことは言うまでもない。そのため、我が国の約99.7%を占める中小企業においては大企業と同様のデジタルツイン実現環境を整備するハードルは非常に高い。そこで、今回の2022年度産業DXアクセラレーションプログラム(以下、産業DX)では、中川ヒューム管工業様とパートナーを組み、製品ヤードでの在庫の効率的な配置管理を実現し、全ステークホルダーの満足度向上を図るための将来的なデジタルツインの構築を目指したシミュレーションの実装を実験的に行うこととした。
企業課題
本取り組みは中川ヒューム管工業株式会社様(以下、N社)がパートナー企業である。N社は、ヒューム管やマンホール等をはじめとしたコンクリート製品の「製造ー販売ー施工」までを手掛け、私たちの日常生活に欠かせない水インフラ設備の基盤となる製品づくりを行っている企業である。
N社が抱える大きな課題の一つが、製造した製品の非効率的な配置管理である。N社の扱うコンクリート製品は400種類を超え、顧客要望に応じた生産計画、工事現場(納品先)の進捗状況による出庫調整等、日々目まぐるしく変化する生産管理の現場では経験則も活用した製品ヤードでの在庫管理が行われている。そのためコンクリート製品特有の課題として製品ヤード内での製品移動はフォークリフトを伴うため容易には行えないなど、効率的な製品配置が出来ない事が以下に挙げるような多くの損失を引き起こすボトルネックとなっている。
- 先入先出ミスによる製品の陳腐化(製品外観の悪化)や補修の発生
- 在庫状況の確認に時間と人を要し、また確認ミスによる製造過不足リスク
- 製品移動に要するコスト、製品破損リスク
- 煩雑なやりとりによる従業員満足度・顧客満足度の低下、等
このように、多くの問題を引き起こしている非効率な製品配置を解決するために、デジタルツインシステム活用への期待が大きい。しかし、本来であれば注文から出庫までの業務フロー全体像を踏まえた検証が無ければ課題を解決する費用対効果の高い効果的なシステムを構築することは難しい。そこで、本取り組みではまずN社が保有する製造と出庫の過去データを用いて、製造された製品の配置とその出庫をシミュレーションし、製品配置の最適化を検証する技術を開発することとした。
データ分析
改めて本取り組みの将来的ビジョンは、製造・出庫予定も反映したヤード内の製品配置の最適化マップを構築し、製品配置の脱属人化を図ることでデジタルツイン化を目指すものである。そして、今回の産業DXでは製造~出庫の業務フローに焦点を当て、非効率な配置管理により起こりうる製品の陳腐化を課題として設定する。その解決方法として、今回はN社が保有する実データに基づく在庫の配置管理における最適化シミュレーションを試みる。
シミュレーション現場
今回は、N社の関東工場の製品置き場において、3種類のヒューム管(A, B, C)を対象にシミュレーションを行う。現場の全体像は図1のとおりであり、その具体的な内容について以下で説明する。
- 4つの大区画の中に、5種類の小区画が存在する
- 大区画
- 各大区画は、配置したヒューム管が「出し入れ可能」な通路(薄黄)、もしくは「出し入れが不可」な通路(グレー)に即する
- 小区画
- 緑の小区画:ヒューム管Aを置くことが可能
- オレンジの小区画:ヒューム管Bを置くことが可能
- 黄の小区画:ヒューム管Cを置くことが可能
- 白の区画:ヒューム管A~Cのいずれか1種類を置くことが可能(ただし、一度いずれかのヒューム管が置かれた時点で、そのヒューム管の区画となる)
- グレーの区画:他の製品が置かれており、対象となるヒューム管は置けない
- 小区画の中には、ヒューム管がピラミッド型に積み上げられている
- 例:最下段に6本、下から2段目に5本、~~~、最上段に1本
- ヒューム管を取り出せる側面は「出し入れ可能」通路のみであるが、出し入れ可能通路に即していても取り出したい製品の手前が他の製品によって防がれている場合には取り出せない
- 例:図1の2行目・2列目の製品を取り出す際には、2行目・1列目の製品がないことが前提
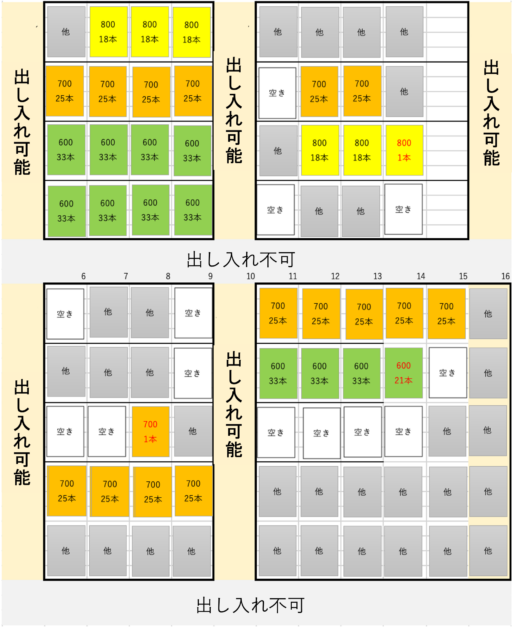
シミュレーション使用データ
今回、シミュレーションの対象とする製品は、数多くある製品の中でヒューム管A, B, Cのみとする。また、シミュレーションに使用するデータは、①2022年3月時点の在庫データ、および②2022年4月から9月の入庫・出庫データとする。
シミュレーションの流れと設定ルール
シミュレーションの流れは、大きく7つのステップで構成されている。1はシミュレーションの初期設定、2~4は入庫に関するシミュレーション、5~7は出庫に関するシミュレーションを指す。
また、その全体の関係性を可視化したものが図2である。
- 在庫を考慮する場合は初期値として配置
- 製品の入庫情報をインプット
- 入庫できる小区画をルール(後述)に従って検索
- 入庫場所・本数の決定
- 製品の出庫情報をインプット
- 求める製品が出庫できる区画を検索
- 出庫場所・本数の決定
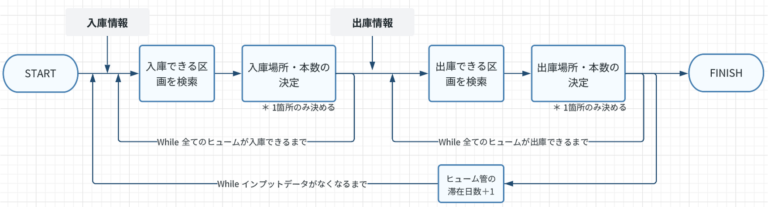
次に、シミュレーションの流れ3に記述したルールについて説明をする。今回のシミュレーションは、2つの方法で小区画に順序を設け、また4つの方法で入庫・出庫のための区画探索を行った。すなわち、全8通り(2×4)でシミュレーションを実施した。ルールの詳細は、以下の通りである。
- 小区画をソートする際のルール(2つ:True, False)
先入先出を行うことを考えた際に、すでにヒューム管Aが置かれている小区画(図1の緑)に積み上げるとピラミッドの下段にある古い製品が取り出せなくなる。何も置かれておらずヒューム管A, B, Cいずれもがおける小区画(図1の白)にヒューム管Aを置くことで先の問題が解決されるように見えるが、その小区画に製品が配置されることで取り出せない製品が発生したり他のヒューム管B, Cの取り出しに影響を与えたりする可能性がある。そこで、今回のシミュレーションでは、実験的にヒューム管Aが置かれている小区画(図1の緑)とヒューム管A, B, Cいずれもがおける小区画(図1の白)の関係性を表す2つのルールを設けた。- True:AとEの要素を区別しないでソート
- False:AとEの要素を区別してソート
- 製品配置に関するルール
- ルール1:距離を測る基準点から近い順に入庫・出庫
- ルール2:区画にある既存のヒューム管本数が多い順に入庫・出庫
- ルール3:区画の既存のヒューム管が少ない順に入庫・出庫
- ルール4:区画の滞在日数合計が小さい順に入庫・出庫
上記に示したルールについて、具体的な例を用いて説明を補足する。
ヒューム管Aを配置する区画を探索する際に対象となる区画は、ヒューム管Aが配置可能な小区画(図1の緑)とヒューム管A, B, Cのいずれかが配置可能な小区画(図1の白)の2つが存在する。この時、集合の要素の数値が小さい方が距離が短いこととする。
- ヒューム管Aが配置可能な小区画(図1の緑)の集合をA = {a2, a5, a6}
- ヒューム管A, B, Cのいずれかが配置可能な小区画(図1の白)の集合をE = {e1, e4}
製品配置に関するルール1を採用した場合に、ヒューム管Aを置く小区画の順序は、
- ルール1・True:{e1, a2, e4, a5, a6}
- ルール1・False:{a2, a5, a6, e1, e4}
となる。そして、それぞれのパターンで定められた順序に従ってヒューム管Aは配置されていくこととなる。
また、評価指標に関しては、ヒューム管の合計滞在日数を採用した。合計滞在日数とは、ある製品が4日間保管された場合には10日間となるように、単純な経過日数ではなく合計日数とした値である。全製品の合計滞在日数が最小となる配置が最適であるといえる。
結果
今回の取り組みでは、在庫を考慮しないシミュレーション1と在庫を考慮するシミュレーション2を行った。
シミュレーション1の結果
シミュレーション1の結果は図3に示すように、もっとも最適であるとされたシミュレーションはルール3とTrueを採用したもの(オレンジライン)であった。2番目に最適であったシミュレーション結果と比較すると、評価指標である合計滞在日数は216,763日の差が出た。ただし、通常保管されている製品の合計滞在日数が明らかでないため、相対的に比較した結果でないことに注意が必要である。
また、今回は将来的にデジタルツインの構築を想定していることから、図4に示すように最終的な各区画の合計滞在日数を可視化も行った。
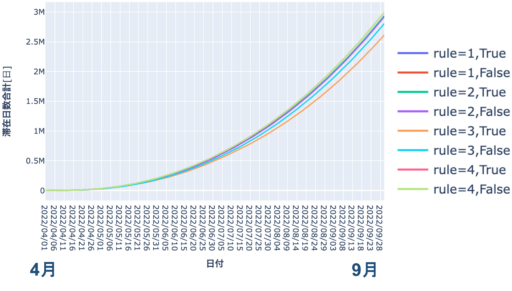
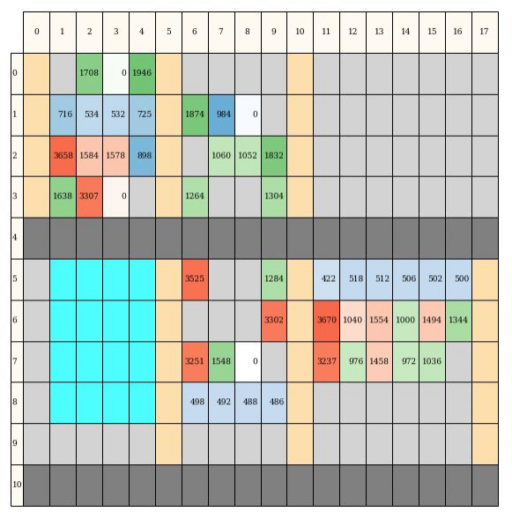
シミュレーション2の結果
シミュレーション2では、より実務でのシミュレーションの実現可能性を高めるために、初期値として在庫データを含めたシミュレーションを行った。その結果、ルール1とFalseを採用したもの、およびルール2とFalseを採用したものについては、シミュレーション結果を算出できた。しかし、図5でエラーの日付が記載されている通り、それ以外の6パターンでは、それぞれ特定の日時で入庫ができない状況となりエラーが発生した。
エラーが発生した原因としては、現在他の製品が置かれているためにヒューム管A~Cがおけないグレーの小区画が不変であったことが考えられる。実務では、他の製品も出庫が行われるためにその区画にどの製品が置かれるかは変わっていくものである。
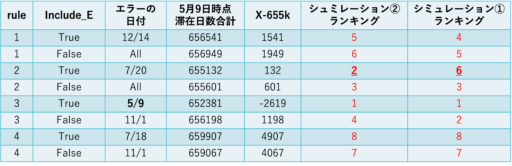
改善点と今後の展望
今回の取り組みでは、過去の製造・出庫の実績データのみでプログラムを試作した。よって、以下の点が大きな改善点として挙げられる。
- 実際にどれだけの製品の陳腐化を防ぐことができたのか比較的に評価できていない
- 製品と区画を限定したシミュレーションであること
- 在庫や区画が柔軟に変化する等の実務の詳細なルール設定が組み込めていない
- 用いた8通りのルール以外のルールについて検討ができていない
今回の産業DXでは、制約条件はあるものの製品配置の可視化マップの生成まで到達している。今後、この成果をベースに注文から出庫までの一連の情報連携に向けた営業・工場の方々とのディスカッションを重ねる事で、シミュレーションの改善に加えて、将来的な組織文化や専門人材の育成等にも通じていくと言える。デジタルツイン活用を目指す活動が技術やシステムの導入だけでなく、経営にも大きく関わってくるものであると明らかにしてくれた事例であると考える。
さいごに
本取り組みをするにあたり、産業DXアクセラレーションプログラムを通じて、約半年間に渡りご協力いただいた中川ヒューム管工業株式会社の皆様にこの場を借りて御礼申し上げます。
また、シミュレーションを行うにあたりコーディングをはじめとする多大な技術的サポートをしてくださった筑波大学社会工学類の中山さん、井福さんにも御礼申し上げます。