Conventional battery test methods measure the stored energy through a full discharge. This procedure is time-consuming and stresses the battery. There is a move towards methods that take only seconds instead of hours; however, rapid testing provides only estimated state-of-health values, and the accuracies vary according to the method used. Public safety, medical and defense organizations still depend on tests involving periodic full discharge/charge cycles.
Battery Analyzer
Battery analyzers became popular in the 1980s and 1990s to restore nickel-cadmium batteries affected by “memory,” as well as to prolong battery life as part of maintenance. The Cadex C7000 Series serves the industry well and set new standards for what a battery analyzer could do. These workhorses accommodate lead-, nickel- and lithium-based batteries, and operate stand-alone or with a PC. Figure 1 illustrates a C7400 battery analyzer servicing a variety of batteries in configured adapters that set the analyzer to the correct setting. Each of the four independent stations allows unique service programs.
Figure 1: Two- and four-station analyzers service batteries from 1.2 to 15V, programmable up to 4A per station. The extended version goes to 36V and 6A charge and discharge currents. The service programs include QuickSort™ for rapid-test Courtesy of Cadex |
Connecting various shapes and forms of batteries has always been a challenge, and technicians have invented unique contraptions with springs and levers so complicated that only the inventor dares to touch. There is no simple way to connect batteries, especially when dealing with small packs that have tiny surface contacts.
Cadex solved the battery interface challenge with custom adapters for common batteries and universal adapters for specialty packs. The custom adapters are easiest to use; they are specially designed and the batteries go in only one way. The adapters are smart and are able to hold configuration codes for up to 10 different battery types. This allows the servicing of batteries with identical footprints but different electrical values. The user can edit the parameters with the menu function on the analyzer or with the PC.
The universal adapters consist of user-programmable Smart Cables that accommodate virtually any battery type. With the proliferation of cellular batteries and the need for a quick and simple battery interchange, Cadex developed the RigidArm™(Figure 2). This adapter features spring-loaded arms that meet the battery contacts from the top down and apply correct pressure to the contacts. Lockable mechanisms allow quick and repetitive testing of same-type batteries. The retractable floor holds the battery in a vertical position, and magnetic guides keep the battery in place if laid horizontally. For added safety, a temperature sensor monitors the battery during the test.
Figure 2: RigidArm™ for cellular batteries The universal adapter simplifies the interface with small batteries. The adapter holds 10 of the most commonly used mAh ratings and is compatible with Cadex battery analyzers. Courtesy of Cadex
|
Servicing Cellular Batteries
Advancements made in battery test equipment make it feasible to service the over four billion cellular batteries in global use at storefronts while the customer waits. Hooking up the battery still needs some skill, and once the contacts are established the service technician may need to enter the capacity in mAh and other battery specifications.
Most cellular batteries have three or four contacts. The positive [+] terminal is normally at the outer edge and the negative [–] one is positioned towards the inside. The third contact is the thermistor measuring the battery temperature, and unless the battery adapter is specially made for the battery type, the thermistor is normally not hooked up for the test; a universal adapter often has its own temperature protection. The fourth contact, if available, may offer code identification for configuration. Figure 3 illustrates a typical contact positioning.
Figure 3: The positive [+] is normally at the outer right and the negative [–] is on the inside. Most batteries have a thermistor; some also offer a code. |
Returned batteries are either discarded or shipped to service centers where they are tested and redistributed as Class B packs. Looking closer at the tonnage of these returned batteries reveals that nine out of 10 packs have no problem and can be serviced. Seeing an opportunity for business, large refurbishing centers have sprung up in the USA that test 400,000 batteries per month, with volumes anticipated to increase to one million per month.
Storefront testing reduces waste, and the motto goes: “To the storefront and no further.” Battery analyzers featuring rapid-test programs are offered that give a clear assessment of a battery in a few seconds while the customer waits. Figure 4 illustrates a service concept for storefront testing while the customer waits. If the battery needs charging or has a genuine fault, an alternate pack is given from the pool of previously tested batteries.
Figure 4: Batteries are serviced while the customer waits. A faulty pack is replaced from the pool of previously serviced batteries. Storefront testing reduces handling, lessens disposal and improves customer satisfaction. Courtesy of Cadex |
One of the difficulties of storefront testing has been the availability of suitable battery diagnostic equipment. The older units lacked accuracy in rapid testing, and had a predictive capacity that resembled a ticket in a Las Vegas lottery; many potential users hesitated to buy such equipment. QuickSort™ provides 90 percent accuracy across the population of cellular batteries. With a PC, some analyzers allow service reports to be printed, and the Internet enables a central manager to monitor the activity of each store. Figure 5 illustrates a battery analyzer designed for storefront use.
Figure 5: Cadex C5100 analyzer for lithium-ion batteries This analyzer rapid tests, charges and cycles batteries. The RigidArm™ adapter allows easy interface to cellular batteries; also accepts preprogrammed adapters. QuickSort™ tests batteries in 30 seconds. Courtesy of Cadex |
Maintaining Fleet Batteries
A battery analyzer assures that fleet batteries meet the minimum performance standards. The device also helps to restore low performers, if such a service is possible with the battery types in question. In addition, a battery analyzer supervises the all-important function of a timely replacement at the end of a productive life. Manufacturers of portable equipment support battery maintenance because well-performing batteries reflect positively on the equipment, a win-win situation for both manufacturer and user.
Many battery analyzers come with PC application software. With BatteryShop™(by Cadex), for example, the PC becomes the command center and all functions are processed through the keyboard, as well as other input devices. Clicking the mouse on any of the 2,000 batteries listed in the database configures the analyzer to the correct setting, eliminating the need for further programming. The user has the liberty to add, remove and edit the batteries listed should the specification change.
Labeling each fleet battery with a permanent ID number simplifies logistics and traceability. A printer connected to PC BatteryShop™ generates these labels in bar code format. The user simply scans the label, which in turn configures the analyzer and retrieves the performance history for review. Besides capacity readings and service dates, purchasing date, vendor information and pricing can also be entered. Figure 6 illustrates the battery scan, service and data examination.
Figure 6: Labeling each battery with a unique number simplifies battery service. Swiping the barcode label reveals the history of the battery. Courtesy of Cadex
|
Another tracking method for fleet batteries is attaching a removable label that shows the battery information at a glance between services, as illustrated in Figure 7. The system is self-governing in that all batteries must regularly be serviced as part of quality control. This is made possible by providing a time period between the last service and the new date due. With this information on hand, the prudent battery user only picks a battery that has been serviced and meets this quality assurance (QA) test protocol. Setting up the maintenance system is simple and managing it requires only about 30 minutes per day.
Figure 7: Sample of removable battery label The label shows battery information at a glance and includes name of organization for traceability, capacity in percent, as well as past and future service dates. |
Setting up a battery maintenance system requires a battery analyzer that is capable of printing battery stick-on labels. The analyzer should also offer a program that automatically restores nickel-based batteries if the set capacity threshold cannot be met. Cadex analyzers meet these requirements and go one step further by offering adjustable capacity target settings to select the minimum performance criteria for the given operation.
Most fleet operations use 80 percent as their battery pass/fail criterion. Increasing the threshold to 85 percent tightens the performance tolerance but passes fewer batteries; lowering the settings extends service life but offers less stringent performance standards. When choosing the setting, the organization must ensure that the lowest-level battery in the fleet is able to fulfill its assigned duty. Figures 8, 9 and 10 illustrate the battery label system.
Rechargeable batteries do not die suddenly but gradually get weaker with time. A service every one to three months offers plenty of confidence that all batteries will meet the minimum required capacity and last through the shift with some energy to spare.
Figure 8: When taking a battery from the charger, the user checks the service date, and if expired the battery is placed in the “To be serviced” box.
| |
Figure 9: The analyzers service the batteries and recondition them if low in capacity (only nickel-based batteries receive recondition). Passing batteries are relabeled showing capacity and the next service date.
| |
Figure 10: The failed batteries are removed from service and replaced with new packs. The new and serviced batteries go back into service by being charged. All figures Courtesy of Cadex |
Battery Test Systems
While battery analyzers are tools to service batteries; battery test systems provide multi-purpose test functions for research laboratories. Typical applications are life cycle testing and verifying cell balance in field imitation. Such tests can often be automated with a custom program. Load capture allows storing load signatures for playback simulations. Many battery test systems also control external load units and environmental chambers. Other uses of such systems are quality inspections and verifying warranty claims. Figure 11 illustrates a typical battery test system.
Figure 11: Four independent channels provide up to 10A each and 36V. Maximum charge power is 400W, discharge is 320W. The discharge power can be enhanced with external load banks. Courtesy of Cadex |
The alternate to a battery test system is a programmable power supply controlled by a computer. Such a platform offers flexibility but requires careful programming to prevent stress to the battery and possible damage or fire if an anomaly were to occur. A battery test system, such as the Cadex C8000, offers protected charge and discharge programs that identify a faulty battery and terminate a service safely. The system can be overridden to do destructive tests.
Simple Guidelines to Choosing a Battery Test System
- Similar to a medical test or the weather forecast, battery testers provide only estimations. No single instrument can do it all; several methods are needed to attain a full assessment.
- Most batteries keep a low internal resistance while the capacity drops gradually with age.
- Battery resistance provides only a snapshot and cannot provide the end-of-life prediction.
- Capacity is the leading health indicator but this measurement is difficult to estimate.
- A charge or discharge agitates the voltage and the battery needs several hours of normalize.
- Coulomb counting requires periodic calibration to keep accuracy.
- Battery management prevents surprise failure and allows for a scheduled retirement.
- Storefront battery testing provides on-site troubleshooting to verify performance.
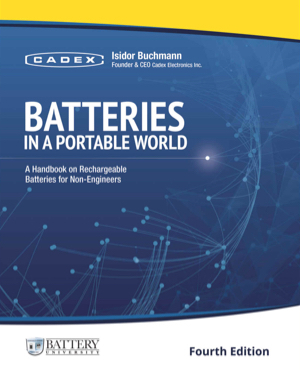
Comments
Looking for comments from the previous website?
Comments from the previous website are not compatible with our new commenting system but we have preserved them so our users can still reference and make use the information in them.