Printed Circuit Board Defect Detection Using Deep Learning via A Skip-Connected Convolutional Autoencoder
- PMID: 34372203
- PMCID: PMC8347834
- DOI: 10.3390/s21154968
Printed Circuit Board Defect Detection Using Deep Learning via A Skip-Connected Convolutional Autoencoder
Abstract
As technology evolves, more components are integrated into printed circuit boards (PCBs) and the PCB layout increases. Because small defects on signal trace can cause significant damage to the system, PCB surface inspection is one of the most important quality control processes. Owing to the limitations of manual inspection, significant efforts have been made to automate the inspection by utilizing high resolution CCD or CMOS sensors. Despite the advanced sensor technology, setting the pass/fail criteria based on small failure samples has always been challenging in traditional machine vision approaches. To overcome these problems, we propose an advanced PCB inspection system based on a skip-connected convolutional autoencoder. The deep autoencoder model was trained to decode the original non-defect images from the defect images. The decoded images were then compared with the input image to identify the defect location. To overcome the small and imbalanced dataset in the early manufacturing stage, we applied appropriate image augmentation to improve the model training performance. The experimental results reveal that a simple unsupervised autoencoder model delivers promising performance, with a detection rate of up to 98% and a false pass rate below 1.7% for the test data, containing 3900 defect and non-defect images.
Keywords: PCB defeat detection; autoencoder; deep learning; detect detection; printed circuit board manufacturing.
Conflict of interest statement
The authors declare no conflict of interest.
Figures
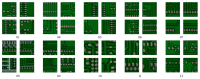
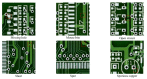
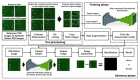
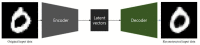
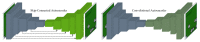
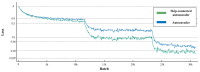
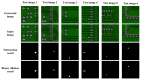
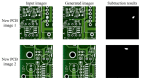
Similar articles
-
Defect Detection in Printed Circuit Boards Using Semi-Supervised Learning.Sensors (Basel). 2023 Mar 19;23(6):3246. doi: 10.3390/s23063246. Sensors (Basel). 2023. PMID: 36991958 Free PMC article.
-
A dataset for deep learning based detection of printed circuit board surface defect.Sci Data. 2024 Jul 22;11(1):811. doi: 10.1038/s41597-024-03656-8. Sci Data. 2024. PMID: 39039085 Free PMC article.
-
Applying deep learning to defect detection in printed circuit boards via a newest model of you-only-look-once.Math Biosci Eng. 2021 May 21;18(4):4411-4428. doi: 10.3934/mbe.2021223. Math Biosci Eng. 2021. PMID: 34198445
-
Printed Circuit Board (PCB) Technology for Electrochemical Sensors and Sensing Platforms.Biosensors (Basel). 2020 Oct 30;10(11):159. doi: 10.3390/bios10110159. Biosensors (Basel). 2020. PMID: 33143106 Free PMC article. Review.
-
Using Deep Learning to Detect Defects in Manufacturing: A Comprehensive Survey and Current Challenges.Materials (Basel). 2020 Dec 16;13(24):5755. doi: 10.3390/ma13245755. Materials (Basel). 2020. PMID: 33339413 Free PMC article. Review.
Cited by
-
Deep learning for differentiating benign from malignant tumors on breast-specific gamma image.Technol Health Care. 2023;31(S1):61-67. doi: 10.3233/THC-236007. Technol Health Care. 2023. PMID: 37038782 Free PMC article.
-
A Novel Feature Extraction Algorithm and System for Flexible Integrated Circuit Packaging Substrate.Micromachines (Basel). 2022 Feb 28;13(3):391. doi: 10.3390/mi13030391. Micromachines (Basel). 2022. PMID: 35334682 Free PMC article.
-
Image-Based Detection of Modifications in Assembled PCBs with Deep Convolutional Autoencoders.Sensors (Basel). 2023 Jan 25;23(3):1353. doi: 10.3390/s23031353. Sensors (Basel). 2023. PMID: 36772392 Free PMC article.
-
Semi-Supervised Defect Detection Method with Data-Expanding Strategy for PCB Quality Inspection.Sensors (Basel). 2022 Oct 19;22(20):7971. doi: 10.3390/s22207971. Sensors (Basel). 2022. PMID: 36298322 Free PMC article.
-
A Robust Deep Learning Ensemble-Driven Model for Defect and Non-Defect Recognition and Classification Using a Weighted Averaging Sequence-Based Meta-Learning Ensembler.Sensors (Basel). 2022 Dec 17;22(24):9971. doi: 10.3390/s22249971. Sensors (Basel). 2022. PMID: 36560340 Free PMC article.
References
-
- Radiant Vision System. [(accessed on 19 July 2021)]; Available online: https://www.radiantvisionsystems.com/products.
-
- Guo F., Guan S.-A. Research of the Machine Vision Based PCB Defect Inspection System; Proceedings of the International Conference on Intelligence Science and Information Engineering; Washington, DC, USA. 20–21 August 2011; pp. 472–475.
-
- Koch J., Gritsch A., Reinhart G. Process design for the management of changes in manufacturing: Toward a Manufacturing Change Management process. CIRP J. Manuf. Sci. Technol. 2016;14:10–19. doi: 10.1016/j.cirpj.2016.04.010. - DOI
-
- Anoop K.P., Kumar S. A Review of PCB Defect Detection Using Image Processing. Intern. J. Eng. Innov. Technol. 2015;4:188–192.
-
- Park J.-K., Kwon B.-K., Park J.-H., Kang D.-J. Machine learning-based imaging system for surface defect inspection. Int. J. Precis. Eng. Manuf. Technol. 2016;3:303–310. doi: 10.1007/s40684-016-0039-x. - DOI
Grants and funding
LinkOut - more resources
Full Text Sources
Other Literature Sources
Research Materials