Fiber Bragg Gratings Sensors for Aircraft Wing Shape Measurement: Recent Applications and Technical Analysis
- PMID: 30583607
- PMCID: PMC6339136
- DOI: 10.3390/s19010055
Fiber Bragg Gratings Sensors for Aircraft Wing Shape Measurement: Recent Applications and Technical Analysis
Abstract
The safety monitoring and tracking of aircraft is becoming more and more important. Under aerodynamic loading, the aircraft wing will produce large bending and torsional deformation, which seriously affects the safety of aircraft. The variation of load on the aircraft wing directly affects the ground observation performance of the aircraft baseline. To compensate for baseline deformations caused by wing deformations, it is necessary to accurately obtain the deformation of the wing shape. The traditional aircraft wing shape measurement methods cannot meet the requirements of small size, light weight, low cost, anti-electromagnetic interference, and adapting to complex environment at the same time, the fiber optic sensing technology for aircraft wing shape measurement has been gradually proved to be a real time and online dynamic measurement method with many excellent characteristics. The principle technical characteristics and bonding technology of fiber Bragg grating sensors (FBGs) are reviewed in this paper. The advantages and disadvantages of other measurement methods are compared and analyzed and the application status of FBG sensing technology for aircraft wing shape measurement is emphatically analyzed. Finally, comprehensive suggestions for improving the accuracy of aircraft wing shape measurement based on FBG sensing technology is put forward.
Keywords: FBGs; accuracy; aircraft; wing shape measurement.
Conflict of interest statement
The author declares no conflict of interest.
Figures
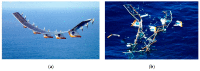
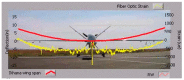
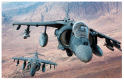
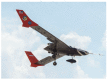
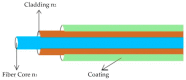
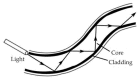
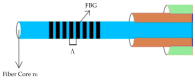
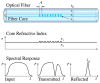
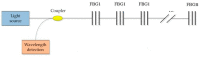
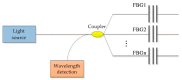
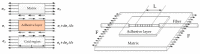
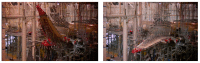
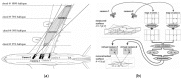
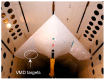
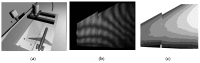
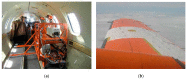
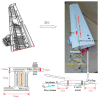
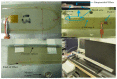
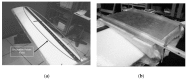
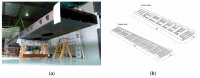
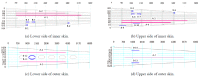
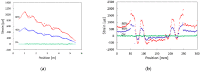
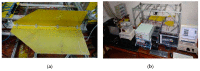
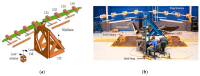
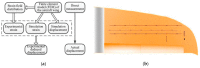
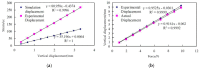
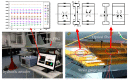
Similar articles
-
Assessment of the Measurement Performance of the Multimodal Fibre Optic Shape Sensing Configuration for a Morphing Wing Section.Sensors (Basel). 2022 Mar 12;22(6):2210. doi: 10.3390/s22062210. Sensors (Basel). 2022. PMID: 35336381 Free PMC article.
-
Sensitivity enhancement of strain sensing utilizing a differential pair of fiber Bragg gratings.Sensors (Basel). 2012;12(4):3891-900. doi: 10.3390/s120403891. Epub 2012 Mar 26. Sensors (Basel). 2012. PMID: 22666008 Free PMC article.
-
Strain Monitoring of a Composite Drag Strut in Aircraft Landing Gear by Fiber Bragg Grating Sensors.Sensors (Basel). 2019 May 15;19(10):2239. doi: 10.3390/s19102239. Sensors (Basel). 2019. PMID: 31096575 Free PMC article.
-
Review of Chirped Fiber Bragg Grating (CFBG) Fiber-Optic Sensors and Their Applications.Sensors (Basel). 2018 Jul 4;18(7):2147. doi: 10.3390/s18072147. Sensors (Basel). 2018. PMID: 29973516 Free PMC article. Review.
-
Fibre Optic Sensors for Structural Health Monitoring of Aircraft Composite Structures: Recent Advances and Applications.Sensors (Basel). 2015 Jul 30;15(8):18666-713. doi: 10.3390/s150818666. Sensors (Basel). 2015. PMID: 26263987 Free PMC article. Review.
Cited by
-
Fused Filament Fabrication of Polymers and Continuous Fiber-Reinforced Polymer Composites: Advances in Structure Optimization and Health Monitoring.Polymers (Basel). 2021 Mar 4;13(5):789. doi: 10.3390/polym13050789. Polymers (Basel). 2021. PMID: 33806621 Free PMC article. Review.
-
Monitoring of a Highly Flexible Aircraft Model Wing Using Time-Expanded Phase-Sensitive OTDR.Sensors (Basel). 2021 May 28;21(11):3766. doi: 10.3390/s21113766. Sensors (Basel). 2021. PMID: 34071642 Free PMC article.
-
Integrated Optical Deformation Measurement with TIR Prism Rods.Sensors (Basel). 2023 Jan 13;23(2):943. doi: 10.3390/s23020943. Sensors (Basel). 2023. PMID: 36679737 Free PMC article.
-
Application of Operational Load Monitoring System for Fatigue Estimation of Main Landing Gear Attachment Frame of an Aircraft.Materials (Basel). 2021 Nov 1;14(21):6564. doi: 10.3390/ma14216564. Materials (Basel). 2021. PMID: 34772089 Free PMC article.
-
The Location Monitoring of Fatigue Crack Damage by Using the Spectral Area Extracted from FBG Spectra.Sensors (Basel). 2020 Apr 22;20(8):2375. doi: 10.3390/s20082375. Sensors (Basel). 2020. PMID: 32331376 Free PMC article.
References
-
- Ko W., Richards W., Tran V. Displacement Theories for In-flight Deformed Shape Predictions of Aerospace Structures. NASA Dryden Flight Research Center; Hampton, VA, USA: 2007.
-
- Ko W., Richards W.U.S. Patent Application for Method for Real-Time Structure Shape-Sensing. No. 7520176. U.S. Patent. 2009 Apr 21;
-
- Pena F., Richards L., Parker A.R., Jr., Piazza A., Chan P., Hamory P. Fiber Optic Sensing System (FOSS) Technology-A New Sensor Paradigm for Comprehensive Structural Monitoring and Model Validation throughout the Vehicle Life-Cycle. [(accessed on 27 October 2018)];2015 Available online: https://ntrs.nasa.gov/archive/nasa/casi.ntrs.nasa.gov/20180007391.pdf.
-
- Military Airspace. [(accessed on 27 October 2018)]; Available online: https://www.militaryaerospace.com/articles/2015/04/ av8b-airplane-blog.html.
-
- Kinet D., Guerra B., Garray D., Caucheteur C., Mgret P. Weakly intrusive optical fibre connector for composite materials applications: Vibration and temperature validation tests; Proceedings of the 5th European Workshop on Optical Fibre Sensors; Krakow, Poland. 19–22 May 2013.
Publication types
LinkOut - more resources
Full Text Sources