Baseline Signal Reconstruction for Temperature Compensation in Lamb Wave-Based Damage Detection
- PMID: 27529245
- PMCID: PMC5017438
- DOI: 10.3390/s16081273
Baseline Signal Reconstruction for Temperature Compensation in Lamb Wave-Based Damage Detection
Abstract
Temperature variations have significant effects on propagation of Lamb wave and therefore can severely limit the damage detection for Lamb wave. In order to mitigate the temperature effect, a temperature compensation method based on baseline signal reconstruction is developed for Lamb wave-based damage detection. The method is a reconstruction of a baseline signal at the temperature of current signal. In other words, it compensates the baseline signal to the temperature of current signal. The Hilbert transform is used to compensate the phase of baseline signal. The Orthogonal matching pursuit (OMP) is used to compensate the amplitude of baseline signal. Experiments were conducted on two composite panels to validate the effectiveness of the proposed method. Results show that the proposed method could effectively work for temperature intervals of at least 18 °C with the baseline signal temperature as the center, and can be applied to the actual damage detection.
Keywords: Hilbert transform; damage detection; lamb waves; orthogonal matching pursuit; temperature compensation.
Figures
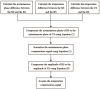
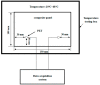
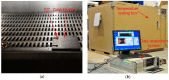


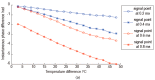
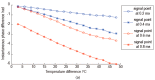
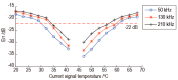
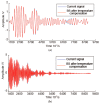
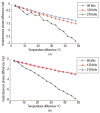
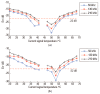
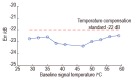
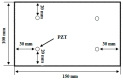

Similar articles
-
Lamb Wave-Based Structural Damage Detection: A Time Series Approach Using Cointegration.Materials (Basel). 2023 Oct 27;16(21):6894. doi: 10.3390/ma16216894. Materials (Basel). 2023. PMID: 37959491 Free PMC article.
-
Identification and Compensation Technique of Non-Uniform Temperature Field for Lamb Wave-and Multiple Sensors-Based Damage Detection.Sensors (Basel). 2019 Jul 2;19(13):2930. doi: 10.3390/s19132930. Sensors (Basel). 2019. PMID: 31269781 Free PMC article.
-
Ultrasound Defect Localization in Shell Structures with Lamb Waves Using Spare Sensor Array and Orthogonal Matching Pursuit Decomposition.Sensors (Basel). 2021 Dec 4;21(23):8127. doi: 10.3390/s21238127. Sensors (Basel). 2021. PMID: 34884131 Free PMC article.
-
Dispersion compensation in Lamb wave defect detection with step-pulse excitation and warped frequency transform.IEEE Trans Ultrason Ferroelectr Freq Control. 2014 Dec;61(12):2075-88. doi: 10.1109/TUFFC.2014.006606. IEEE Trans Ultrason Ferroelectr Freq Control. 2014. PMID: 25474782
-
Lamb Wave Based Structural Damage Detection Using Stationarity Tests.Materials (Basel). 2021 Nov 12;14(22):6823. doi: 10.3390/ma14226823. Materials (Basel). 2021. PMID: 34832225 Free PMC article.
Cited by
-
A Quantitative Approach for the Bone-implant Osseointegration Assessment Based on Ultrasonic Elastic Guided Waves.Sensors (Basel). 2019 Jan 22;19(3):454. doi: 10.3390/s19030454. Sensors (Basel). 2019. PMID: 30678295 Free PMC article.
-
Lamb Wave-Based Structural Damage Detection: A Time Series Approach Using Cointegration.Materials (Basel). 2023 Oct 27;16(21):6894. doi: 10.3390/ma16216894. Materials (Basel). 2023. PMID: 37959491 Free PMC article.
-
Wave Propagation in Aluminum Honeycomb Plate and Debonding Detection Using Scanning Laser Vibrometer.Sensors (Basel). 2018 May 23;18(6):1669. doi: 10.3390/s18061669. Sensors (Basel). 2018. PMID: 29789509 Free PMC article.
-
FEM Simulation-Based Adversarial Domain Adaptation for Fatigue Crack Detection Using Lamb Wave.Sensors (Basel). 2023 Feb 9;23(4):1943. doi: 10.3390/s23041943. Sensors (Basel). 2023. PMID: 36850542 Free PMC article.
-
A New Approach to Guided Wave Ray Tomography for Temperature-Robust Damage Detection Using Piezoelectric Sensors.Sensors (Basel). 2018 Oct 18;18(10):3518. doi: 10.3390/s18103518. Sensors (Basel). 2018. PMID: 30340401 Free PMC article.
References
-
- Hu N., Shimomukai T., Fukunaga H., Su Z.Q. Damage identification of metallic structures using A0 mode of Lamb wave. Struct. Health Monit. 2008;7:271–285.
-
- Mujica L.E., Vehi J., Ruiz M., Verleysen M., Staszewski W., Worden K. Multivariate statistics process control for dimensionality reduction in structural assessment. Mech. Syst. Signal Process. 2008;22:155–171. doi: 10.1016/j.ymssp.2007.05.001. - DOI
-
- Sharif-Khodaei Z., Aliabadi M.H. Assessment of delay-and-sum algorithms for damage detection in aluminium and composite plates. Smart Mater. Struct. 2014;23:628–634. doi: 10.1088/0964-1726/23/7/075007. - DOI
LinkOut - more resources
Full Text Sources
Other Literature Sources