Stretchable and flexible high-strain sensors made using carbon nanotubes and graphite films on natural rubber
- PMID: 24399158
- PMCID: PMC3926590
- DOI: 10.3390/s140100868
Stretchable and flexible high-strain sensors made using carbon nanotubes and graphite films on natural rubber
Abstract
Conventional metallic strain sensors are flexible, but they can sustain maximum strains of only ~5%, so there is a need for sensors that can bear high strains for multifunctional applications. In this study, we report stretchable and flexible high-strain sensors that consist of entangled and randomly distributed multiwall carbon nanotubes or graphite flakes on a natural rubber substrate. Carbon nanotubes/graphite flakes were sandwiched in natural rubber to produce these high-strain sensors. Using field emission scanning electron microscopy, the morphology of the films for both the carbon nanotube and graphite sensors were assessed under different strain conditions (0% and 400% strain). As the strain was increased, the films fractured, resulting in an increase in the electrical resistance of the sensor; this change was reversible. Strains of up to 246% (graphite sensor) and 620% (carbon nanotube sensor) were measured; these values are respectively ~50 and ~120 times greater than those of conventional metallic strain sensors.
Figures
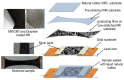
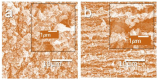
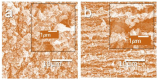
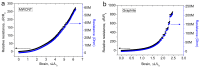
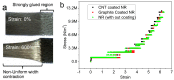
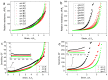
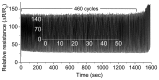

Similar articles
-
A stretchable carbon nanotube strain sensor for human-motion detection.Nat Nanotechnol. 2011 May;6(5):296-301. doi: 10.1038/nnano.2011.36. Epub 2011 Mar 27. Nat Nanotechnol. 2011. PMID: 21441912
-
Ultra-stretchable and skin-mountable strain sensors using carbon nanotubes-Ecoflex nanocomposites.Nanotechnology. 2015 Sep 18;26(37):375501. doi: 10.1088/0957-4484/26/37/375501. Epub 2015 Aug 25. Nanotechnology. 2015. PMID: 26303117
-
Flexible field emission of nitrogen-doped carbon nanotubes/reduced graphene hybrid films.Small. 2011 Jan 3;7(1):95-100. doi: 10.1002/smll.201001168. Small. 2011. PMID: 21104826
-
Chemical functionalization of carbon nanotubes.J Nanosci Nanotechnol. 2002 Apr;2(2):113-23. doi: 10.1166/jnn.2002.107. J Nanosci Nanotechnol. 2002. PMID: 12908295 Review.
-
Electronic and photonic properties of doped carbon nanotubes.J Nanosci Nanotechnol. 2003 Dec;3(6):459-78. doi: 10.1166/jnn.2003.241. J Nanosci Nanotechnol. 2003. PMID: 15002124 Review.
Cited by
-
Graphene and Its Derivatives: Synthesis and Application in the Electrochemical Detection of Analytes in Sweat.Biosensors (Basel). 2022 Oct 21;12(10):910. doi: 10.3390/bios12100910. Biosensors (Basel). 2022. PMID: 36291046 Free PMC article. Review.
-
Nanomaterials-patterned flexible electrodes for wearable health monitoring: a review.J Mater Sci. 2021;56(27):14900-14942. doi: 10.1007/s10853-021-06248-8. Epub 2021 Jun 28. J Mater Sci. 2021. PMID: 34219807 Free PMC article. Review.
-
Design and Optimization of Piezoresistive PEO/PEDOT:PSS Electrospun Nanofibers for Wearable Flex Sensors.Nanomaterials (Basel). 2020 Oct 30;10(11):2166. doi: 10.3390/nano10112166. Nanomaterials (Basel). 2020. PMID: 33143003 Free PMC article.
-
The Numerical and Experimental Investigation of Piezoresistive Performance of Carbon Nanotube/Carbon Black/Polyvinylidene Fluoride Composite.Materials (Basel). 2023 Aug 11;16(16):5581. doi: 10.3390/ma16165581. Materials (Basel). 2023. PMID: 37629871 Free PMC article.
-
Structure-Property Relationships in Graphene-Based Strain and Pressure Sensors for Potential Artificial Intelligence Applications.Sensors (Basel). 2019 Mar 12;19(5):1250. doi: 10.3390/s19051250. Sensors (Basel). 2019. PMID: 30871069 Free PMC article. Review.
References
-
- Moshfegh S., Ebrahimi N. Strain sensors based on graphite fillers. Iran Polym. J. 2004;13:113–119.
-
- Dobie W.B., Isaac P.C.G. Electric Resistance Strain Gauges. English Universities Press Limited; Madison, WI, USA: 1948.
-
- Hu B., Chen W., Zhou J. High performance flexible sensor based on inorganic nanomaterials. Sens. Actuators B: Chem. 2013;176:522–533.
-
- Zou J.-F., Yu Z.-Z., Pan Y.-X., Fang X.-P., Ou Y.-C. Conductive mechanism of polymer/graphite conducting composites with low percolation threshold. J. Polym. Sci. Part B: Polym. Phys. 2002;40:954–963.
-
- Wang L., Ding T., Wang P. Thin flexible pressure sensor array based on carbon black/silicone rubber nanocomposite. IEEE Sens. J. 2009;9:1130–1135.
Publication types
MeSH terms
Substances
LinkOut - more resources
Full Text Sources
Other Literature Sources
Research Materials