Temperature effects and compensation-control methods
- PMID: 22408509
- PMCID: PMC3292111
- DOI: 10.3390/s91008349
Temperature effects and compensation-control methods
Abstract
In the analysis of the effects of temperature on the performance of microgyroscopes, it is found that the resonant frequency of the microgyroscope decreases linearly as the temperature increases, and the quality factor changes drastically at low temperatures. Moreover, the zero bias changes greatly with temperature variations. To reduce the temperature effects on the microgyroscope, temperature compensation-control methods are proposed. In the first place, a BP (Back Propagation) neural network and polynomial fitting are utilized for building the temperature model of the microgyroscope. Considering the simplicity and real-time requirements, piecewise polynomial fitting is applied in the temperature compensation system. Then, an integral-separated PID (Proportion Integration Differentiation) control algorithm is adopted in the temperature control system, which can stabilize the temperature inside the microgyrocope in pursuing its optimal performance. Experimental results reveal that the combination of microgyroscope temperature compensation and control methods is both realizable and effective in a miniaturized microgyroscope prototype.
Keywords: BP neural networks; microgyroscope; polynomial fitting; temperature characteristic; temperature compensation and control.
Figures
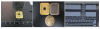
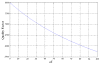
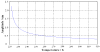
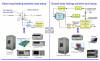
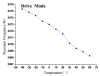
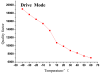
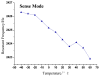
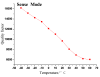
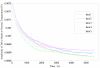
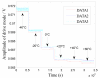
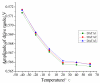
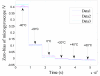
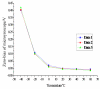
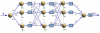
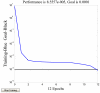
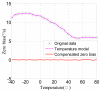
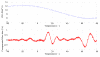
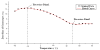
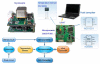
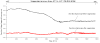
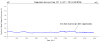
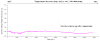
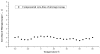
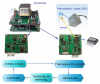
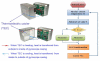

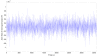
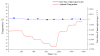
Similar articles
-
Development of a prototype miniature silicon microgyroscope.Sensors (Basel). 2009;9(6):4586-605. doi: 10.3390/s90604586. Epub 2009 Jun 11. Sensors (Basel). 2009. PMID: 22408543 Free PMC article.
-
Temperature Compensation Method Based on an Improved Firefly Algorithm Optimized Backpropagation Neural Network for Micromachined Silicon Resonant Accelerometers.Micromachines (Basel). 2022 Jun 30;13(7):1054. doi: 10.3390/mi13071054. Micromachines (Basel). 2022. PMID: 35888869 Free PMC article.
-
Temperature Compensation of Elasto-Magneto-Electric (EME) Sensors in Cable Force Monitoring Using BP Neural Network.Sensors (Basel). 2018 Jul 6;18(7):2176. doi: 10.3390/s18072176. Sensors (Basel). 2018. PMID: 29986439 Free PMC article.
-
Compensation of Rotary Encoders Using Fourier Expansion-Back Propagation Neural Network Optimized by Genetic Algorithm.Sensors (Basel). 2020 May 3;20(9):2603. doi: 10.3390/s20092603. Sensors (Basel). 2020. PMID: 32375212 Free PMC article.
-
Kinetic and thermodynamic compensation. A current and practical review for foods.Food Res Int. 2017 Jun;96:132-153. doi: 10.1016/j.foodres.2017.03.004. Epub 2017 Mar 6. Food Res Int. 2017. PMID: 28528093 Review.
Cited by
-
Machine Learning and Swarm Optimization Algorithm in Temperature Compensation of Pressure Sensors.Sensors (Basel). 2022 Oct 29;22(21):8309. doi: 10.3390/s22218309. Sensors (Basel). 2022. PMID: 36366005 Free PMC article.
-
Application of PSO-BPNN-PID Controller in Nutrient Solution EC Precise Control System: Applied Research.Sensors (Basel). 2022 Jul 24;22(15):5515. doi: 10.3390/s22155515. Sensors (Basel). 2022. PMID: 35898019 Free PMC article.
-
A Temperature Control Method for Microaccelerometer Chips Based on Genetic Algorithm and Fuzzy PID Control.Micromachines (Basel). 2021 Dec 4;12(12):1511. doi: 10.3390/mi12121511. Micromachines (Basel). 2021. PMID: 34945361 Free PMC article.
-
Fusion of Unobtrusive Sensing Solutions for Sprained Ankle Rehabilitation Exercises Monitoring in Home Environments.Sensors (Basel). 2021 Nov 13;21(22):7560. doi: 10.3390/s21227560. Sensors (Basel). 2021. PMID: 34833636 Free PMC article.
-
Consideration of Thermo-Vacuum Stability of a MEMS Gyroscope for Space Applications.Sensors (Basel). 2020 Dec 15;20(24):7172. doi: 10.3390/s20247172. Sensors (Basel). 2020. PMID: 33333719 Free PMC article.
References
-
- Sharma A., Zaman M.F., Ayazi F. A 0.2 °/hr micro-gyroscope with automatic CMOS mode matching. Proceedings of the IEEE International Solid-State Circuits Conference; San Francisco, CA, USA. 2007. pp. 386–387.
-
- Kulygin A., Schmid U., Seidel H. Characterization of a novel micromachined gyroscope under varying ambient pressure conditions. Sens. Actuat. A. 2008:145–146. 52–58.
-
- Li Z., Yang Z., Xiao Z. A bulk micromachined vibratory lateral gyroscope fabricated with wafer bonding and deep trench etching. Sens. Actuat. 2000;83:24–29.
-
- Li W.Y., Ruan A.W., Luo J.S. Error sources in micromachined comb-drive turning-fork gyroscope. J. Aeronaut. Astronaut. 1999;20:426–429.
-
- Ashwin A.S. Integrated Micromechanical Resonant Sensor for Inertial Measurement System. School of Electrical Engineering and Computer Science, University of California Berkeley; Berkeley, CA, USA: 2002.
LinkOut - more resources
Full Text Sources
Other Literature Sources