Electromagnetic imaging methods for nondestructive evaluation applications
- PMID: 22247693
- PMCID: PMC3252010
- DOI: 10.3390/s111211774
Electromagnetic imaging methods for nondestructive evaluation applications
Abstract
Electromagnetic nondestructive tests are important and widely used within the field of nondestructive evaluation (NDE). The recent advances in sensing technology, hardware and software development dedicated to imaging and image processing, and material sciences have greatly expanded the application fields, sophisticated the systems design and made the potential of electromagnetic NDE imaging seemingly unlimited. This review provides a comprehensive summary of research works on electromagnetic imaging methods for NDE applications, followed by the summary and discussions on future directions.
Keywords: electromagnetic imaging; nondestructive evaluation; noninvasive imaging; structural health monitoring.
Figures
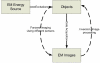
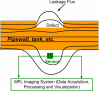
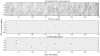
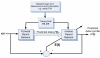
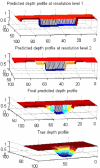
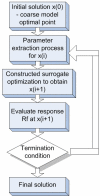
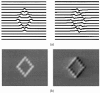
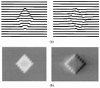
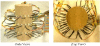
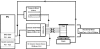
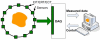
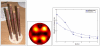
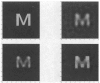
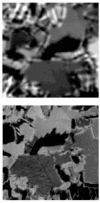
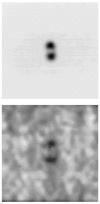
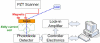
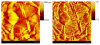
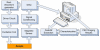
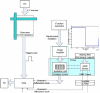
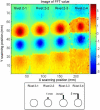
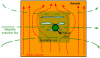
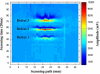
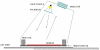
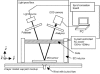
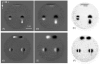
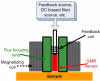
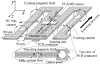
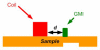
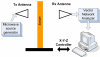
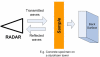

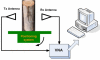
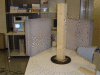
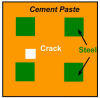
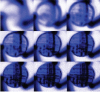
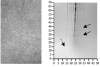
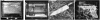
Similar articles
-
Electromagnetic pulsed thermography for natural cracks inspection.Sci Rep. 2017 Feb 7;7:42073. doi: 10.1038/srep42073. Sci Rep. 2017. PMID: 28169361 Free PMC article.
-
Multi-wave and hybrid imaging techniques: a new direction for nondestructive testing and structural health monitoring.Sensors (Basel). 2013 Nov 27;13(12):16146-90. doi: 10.3390/s131216146. Sensors (Basel). 2013. PMID: 24287536 Free PMC article. Review.
-
Basic principles of magnetic resonance imaging.Neuroimaging Clin N Am. 2008 Nov;18(4):623-36, x. doi: 10.1016/j.nic.2008.06.004. Neuroimaging Clin N Am. 2008. PMID: 19068405 Review.
-
Automation and system integration of scanning tomographic acoustic microscope.Comput Med Imaging Graph. 1997 Sep-Oct;21(5):265-76. doi: 10.1016/s0895-6111(97)00017-7. Comput Med Imaging Graph. 1997. PMID: 9475432
-
Smartphone-based imaging systems for medical applications: a critical review.J Biomed Opt. 2021 Apr;26(4):040902. doi: 10.1117/1.JBO.26.4.040902. J Biomed Opt. 2021. PMID: 33860648 Free PMC article. Review.
Cited by
-
Analysis and design of holographic magnetic metasurfaces in the very near field for sensing applications at quasi-static regime.Sci Rep. 2023 Jun 7;13(1):9220. doi: 10.1038/s41598-023-36452-2. Sci Rep. 2023. PMID: 37286725 Free PMC article.
-
CMOS Detector Staggered Array Module for Sub-Terahertz Imaging on Conveyor Belt System.Sensors (Basel). 2023 Jan 20;23(3):1232. doi: 10.3390/s23031232. Sensors (Basel). 2023. PMID: 36772271 Free PMC article.
-
Electromagnetic field analysis and modeling of a relative position detection sensor for high speed maglev trains.Sensors (Basel). 2012;12(5):6447-62. doi: 10.3390/s120506447. Epub 2012 May 15. Sensors (Basel). 2012. PMID: 22778652 Free PMC article.
-
A Portable Electromagnetic System Based on mm-Wave Radars and GNSS-RTK Solutions for 3D Scanning of Large Material Piles.Sensors (Basel). 2021 Jan 23;21(3):757. doi: 10.3390/s21030757. Sensors (Basel). 2021. PMID: 33498696 Free PMC article.
-
New Proposal for Inverse Algorithm Enhancing Noise Robust Eddy-Current Non-Destructive Evaluation.Sensors (Basel). 2020 Sep 28;20(19):5548. doi: 10.3390/s20195548. Sensors (Basel). 2020. PMID: 32998312 Free PMC article.
References
-
- Tricoles G., Farhat N.H. Microwave holography: Applications and techniques. Proc. IEEE. 1977;65:108–121.
-
- Deng Y. Michigan State University; East Lansing, MI, USA: 2009. Forward and Inverse Problems in Noninvasive Imaging Techniques. Ph.D. Thesis,
-
- Achenbach J. Quantitative nondestructive evaluation. Int. J. Solids Struct. 2000;37:13–27.
-
- Jiles D.C. Review of magnetic methods for nondestructive evaluation. NDT Int. 1988;21:311–319.
Publication types
MeSH terms
LinkOut - more resources
Full Text Sources
Other Literature Sources